The surge impedance loading (SIL) of a line is the power load at which the net reactive power is zero. So, if your transmission line wants to "absorb" reactive power, the SIL is the amount of reactive power you would have to produce to balance it out to zero. You can calculate it by dividing the square of the line-to-line voltage by the line's characteristic impedance.
As per Torque/Slip characteristic for AC Motor, the value of the Max. Torque can be developed is constant while the Starting Torque occurs @ S=.1, (T proportional to r2 and S also proportional to r2 where r2 is the rotor resistance, the ratio r2/x2 when equal to 1 gives the max. Torque w.r.t Slip at Starting. Wound rotor motors are suitable and recommended for application for MV drive where it is required to be started on load such as ID. Fans, S.D Fans, Drill, etc.
For now I am working on a mining project which involves starting two SAG mills, the method of starting these mills is by rotor resistance and likewise we are using an energy recovery system (SER), could someone tell me how this system works SER? Each mills have two motors of 8000 kW at 13.8 kV.
There is a ANSI/IEEE standard that defines the standard number identification for electrical devices. You will find that some of the more common ones are 50 over current, 51 short terms over current, 27 under voltage, 59 over voltage, and 50G ground over current detection relay.
In 3 leg three phase transformer, do we get some phase voltage magnitude and angle change due to un-symmetrical reluctance seen by every different phases? The phase at the middle leg is not distorted because fluxes come from both rear legs equally in magnitude. But voltage and angle of rear legs change somewhat because the other two phases' flux come to rear legs in different magnitudes. So this distorts both magnitude and angle of voltage.
As far as the cables insulation material is concerned, EPR and XLPE insulated cables to some extent are having similar properties. In this respect, there are different types of Electrical cables such as ETFE ,FP, HOFR , LSF,LSOH, MI, PILC, TRS, VR, CTS, CSP, PTFE, etc.
There are hundreds of applications for a frequency inverter. I use them on a pump to test pumps with voltages from 208-600VAC 3PH 50 and 60 HZ. You just have to size the frequency inverter to the largest 208 HP motor, so it can handle the current. Many people are installing them on pumps, fans and air compressors to get the energy savings of lowering the speed on the motor to maintain the pressure, temperature and flow.
Variable frequency drives are important power electronic devices. When we start an electric motor, we are increasing from 0 speed to full operating speed. A VFD ensures that the motor accelerates (increases its speed) to its full speed in a smooth manner, without causing much irregularities. In other words, VFDs make the motor accelerate uniformly.
VFDs are also easy to install and use. VFD drives are not only for starting motors (like the normal starters), but for easy speed control as well.
At zero speed the motor requires torque which is flux (voltage) and current (mostly reactive). Only a little bit of active current to compensate for the motor power losses.
Only the power losses need to be drawn from the grid at that time, which means a very small amount of current. It may produce 200% current on the motor and pull only 10% current from the grid.
Only the power losses need to be drawn from the grid at that time, which means a very small amount of current. It may produce 200% current on the motor and pull only 10% current from the grid.
Variable frequency drive is capable to smoothly starting AC motors (ramp from 0 up to 100% of the load) as well as the energy saving will be achieved, accordingly. Also may I confirmed that VFD also acting as AC Motor starting means among (Star/Delta, Soft Starter, Auto Transformer, Electrolyte, series resistance - wound rotor- etc,). The starting factor of VFD drive is usually 1 up to 1.2 with respect to the rated load current while for Direct On line about 5-6.
In this method, when the voltage sag causes the variable frequency drive to reach its undervoltage trip level, the VFD drive will shut off the inverter section and thus remove power from the motor instead of tripping. The motor will coast down during the duration of the sag and, as soon as the voltage recovers, the VFD will start into the still-spinning motor and ramp up to set speed.
What will happen when we back-charge 220 kV / 20 kV, 500 MVA Generator transformer through 75 MVA, 220/132 kV Grid Auto Transformer. Whether the 75 MVA Grid Auto Transformer can successfully back-charge the 500 MVA Generator transformer? If not, what can be the optimum transformer size to back-charge the 500 MVA Generator transformer.
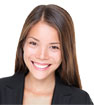
Featured
Like pumps, fans consume significant electrical energy while serving several applications. In many plants, the VFDs (variable ...
A frequency inverter controls AC motor speed. The frequency inverter converts the fixed supply frequency (60 Hz) to a ...
Motor starter (also known as soft starter, motor soft starter) is a electronic device integrates soft start, soft stop, ...
Soft starter allows the output voltage decreases gradually to achieve soft stop, in order to protect the equipment. Such as the ...
Soft Starter reduces electric motor starting current to 2-4 times during motor start up, reduces the impact to power grid during ...

In Discussion
Electrical generation
Good motor school or workshop
What safety systems to be used inside pump room and tank?
Solar park wind loads
Difference between Flyback topology and Coupled-Inductors Boost topology
Optical Isolation for 4-20ma
Importance of Retension/residence time?
Induction motor replace with BLDC motor
Good motor school or workshop
What safety systems to be used inside pump room and tank?
Solar park wind loads
Difference between Flyback topology and Coupled-Inductors Boost topology
Optical Isolation for 4-20ma
Importance of Retension/residence time?
Induction motor replace with BLDC motor