As you know the inductance of SRM depends on two parameters: 1.coil current 2.rotor position .it means that you have a lot of possible situation that each situation has particular value of inductance .if you want to measure inductance at particular position, I think you should excite one phase with ac supply and use circuit equations (kvl) to find inductance. if you use a dc supply you should measure the flux and it's hard to do.
If the material is non-grain-oriented, the path of least resistance for the magnetic flux varies widely from point to point across the sheet.
If the material is grain-oriented, the material is aligned such that there is a significant reduction in the energy requirement for passing flux in one direction relative to any other.
If the material is grain-oriented, the material is aligned such that there is a significant reduction in the energy requirement for passing flux in one direction relative to any other.
The method of creating a die-cast rotor is as follows:
1. An assembly of steel laminations (which may or may not be grain-oriented) containing the openings for both rotor bars and ventilation (as required) is made and clamped together to form a cylindrical iron core.
2. The assembly is inserted into a mold, which has space both above and below the core for the end (shorting) ring assembly.
1. An assembly of steel laminations (which may or may not be grain-oriented) containing the openings for both rotor bars and ventilation (as required) is made and clamped together to form a cylindrical iron core.
2. The assembly is inserted into a mold, which has space both above and below the core for the end (shorting) ring assembly.
Most electrical steels used in stator and rotor construction also have an insulating coating applied; some of these are organic materials and some are inorganic (solvent-based) materials. The choice is typically made based on a combination of temperature gradient and local environmental laws. The inorganic (solvent) materials can generally withstand higher temperatures but are far less eco-friendly in the manufacture of the coating material or in the curing of the coating after it is applied.
This is a very simplified comparison for a very complex issue. Every manufacturer is somewhat different in their approach, and there are literally thousands of design details in each machine that can be accommodated as the designer balances efficiency VS performance VS cost VS reliability VS safety VS manufacturability.
The PLC languages themselves are fairly similar between different manufacturers. You basically have ladder logic (which looks like a relay contact map), function blocks (which are more akin to an electronic circuit overview) and structured language (of which there are several variants. Most look a lot like high-level programming languages). You might encounter some functions having different names or in-/outputs between manufacturers but most of them look much the same.
MCC is shorted for Motor Control Center. Soft starter MCC control cabinet consists of the following components: (1) input circuit breaker, (2) Soft starter (including electronic control circuit and three phase thyristor), (3) soft starter bypass contactor, (4 ) secondary-side control circuit (for manual start, remote start, soft start and direct start functions selection and operation), and voltage, current display, fault, running and working status indicators.
Overload protection: the soft starter has current control loop to track and detect of the changes of the electric motor current. Achieve overload protection by increasing overload current settings and inverse time control mode, to cut down the thyristor and send alarm signals when motor is overload.
In electric motor stop, the traditional control ways are accomplished by momentary power cutting off. But in lots of applications, it's not allowed the motor instant shutdown. For example: high-rise buildings, building's water pump system, it will appear huge water hammer during instant shutdown, to damage the pipe, even the pumps. To reduce and avoid "water hammer" phenomenon, the pumps motor need be shut down gradually, that is soft stop.
Induction motor is inductive load, the current lags the voltage, most electrical appliances are the same. In order to improve the power factor we need to use capacitive load for compensation, parallel capacitors or with synchronous motor for compensation. Reduce motor excitation current also can improve the power factor.
I have a generator of 3 hp, and it outputs 230 V, and I have a submersible Electric Pump, the motor of which is rated to operate at 460 V, Can I use a step up transformer to increase the voltage output from my generator and power the pump? What more parameters do I need to know of in this case?
Motor starter (also known as soft starter, motor soft starter) is a electronic device integrates soft start, soft stop, light-load energy saving and various protection functions for motor controls. Its main components are the three phase reverse parallel thyristors between power supply and being controlled motor and related control circuits. Control the conduction angle of the three phase reverse parallel thyristors by different methods, to achieve different functions by the changeable of the input voltage on the controlled motors.
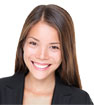
Featured
Like pumps, fans consume significant electrical energy while serving several applications. In many plants, the VFDs (variable ...
A frequency inverter controls AC motor speed. The frequency inverter converts the fixed supply frequency (60 Hz) to a ...
Motor starter (also known as soft starter, motor soft starter) is a electronic device integrates soft start, soft stop, ...
Soft starter allows the output voltage decreases gradually to achieve soft stop, in order to protect the equipment. Such as the ...
Soft Starter reduces electric motor starting current to 2-4 times during motor start up, reduces the impact to power grid during ...

In Discussion
How to select the best control valve?
Does anyone know what is life cycle for solar panel?
PUMP SELECTION - How can i increase my NPSH margin ?
flyback converter design
One cycle control for PFC or general DC/DC?
Can the rotor resistance drop down from its design value?
Cu320-2 PN
PID control in DCS systems
Does anyone know what is life cycle for solar panel?
PUMP SELECTION - How can i increase my NPSH margin ?
flyback converter design
One cycle control for PFC or general DC/DC?
Can the rotor resistance drop down from its design value?
Cu320-2 PN
PID control in DCS systems