Home » Blog
Well first let get one thing straight for transformers: the higher the line frequency, the lower the core (iron) losses! The core power loss are proportional to kf*B^2 approximately for any machine, dynamic or static. But transformers are self-excited static machines, meaning the flux density B is reverse proportional to the line frequency, therefore Pcoreloss = kB^2*f=k*(1/f)^2*f=k/f... so the higher f, the lower the losses. However, increasing the frequency also increases the magnetizing inductance - lowering the magnetizing current. For if you increase the frequency you may want to increase the voltage. But of course this is not usually practical, as line voltage of 60Hz systems is usually lower than those of 50Hz systems. So operating a 50Hz transformer at 60Hz should be safe, but may result in higher voltage drop because of lower magnetizing current and because of higher leakage inductance (the series inductance).
I've seen some attempt of electrical driven prototypes in the field, but
is still not an enough big sector that let you find specific
literature. Excluding the large dumpers for mining, probably the only
machine that is built in series is D7E from CAT.
One of largest engineering challenge that you will face on a similar application, is the cooling to the power electronic. You can consider that you will have to dissipate 3-5% of the power that your driver is processing and the max temperature of IGBT's is not so far from the max temperature in that your vehicle can operate. A small temperature delta, mean a large heat exchanger and/or pretty high speed of air through it. (That with all the problems related to that). A possible solution is liquid cool the IGBT's mounting them on the aluminum plate. You can't use the engine cooling fluid because it too warm, but you may can use hydraulic oil (that should never get warmer of 55C).
One of largest engineering challenge that you will face on a similar application, is the cooling to the power electronic. You can consider that you will have to dissipate 3-5% of the power that your driver is processing and the max temperature of IGBT's is not so far from the max temperature in that your vehicle can operate. A small temperature delta, mean a large heat exchanger and/or pretty high speed of air through it. (That with all the problems related to that). A possible solution is liquid cool the IGBT's mounting them on the aluminum plate. You can't use the engine cooling fluid because it too warm, but you may can use hydraulic oil (that should never get warmer of 55C).
Advantages: Clearly, this Special Protection System saved the day, and
bought time until an additional line was added 4 years later.
Disadvantages: The downside was the challenge of installing and testing such a complicated scheme with the potential for mis-operation. I don't recall any mis-operations occurring, but it was still a bit "dicey". I have been at that same plant during a full load unit trip (Generator differential) and it was an "exciting" experience to say the least! While I did recommend that we conduct a "live test" to see what would really happen and perhaps test our system BLACK START procedures, this suggestion was not well received by management (LOL).
Disadvantages: The downside was the challenge of installing and testing such a complicated scheme with the potential for mis-operation. I don't recall any mis-operations occurring, but it was still a bit "dicey". I have been at that same plant during a full load unit trip (Generator differential) and it was an "exciting" experience to say the least! While I did recommend that we conduct a "live test" to see what would really happen and perhaps test our system BLACK START procedures, this suggestion was not well received by management (LOL).
When synchronous generators (alternators) are connected in parallel with
each other on an AC grid, they are all operating at a speed that is
directly proportional to the frequency of the AC grid. No generator can
go faster or slower than the speed which is proportional to the
frequency.
That is, when a synchronous generator and its prime mover is operated in parallel with other synchronous generators and their prime movers, the speed of all of the generator rotors (and hence their prime movers if directly coupled to the generator rotors) is fixed by the frequency of the grid. If the grid frequency goes up, the speed of all the generator rotors goes up at the same time. Conversely, if the grid frequency goes down, the speed of all the generator rotors goes down at the same time. It is the job of the grid/system operators to control the amount of generation so that it exactly matches the load on the system so that the frequency remains relatively constant.
That is, when a synchronous generator and its prime mover is operated in parallel with other synchronous generators and their prime movers, the speed of all of the generator rotors (and hence their prime movers if directly coupled to the generator rotors) is fixed by the frequency of the grid. If the grid frequency goes up, the speed of all the generator rotors goes up at the same time. Conversely, if the grid frequency goes down, the speed of all the generator rotors goes down at the same time. It is the job of the grid/system operators to control the amount of generation so that it exactly matches the load on the system so that the frequency remains relatively constant.
The basic configuration of a variable frequency drive is as follows.
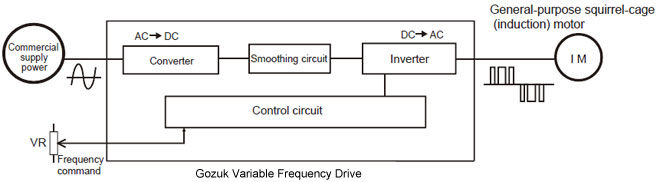
Fig. 1 Basic configuration of variable frequency drive
Each part of a variable frequency drive has the following function.
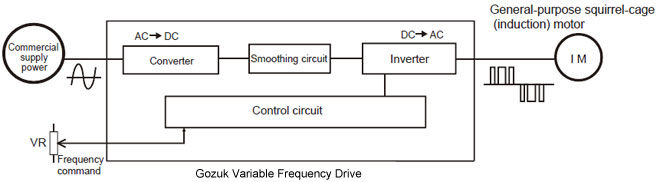
Fig. 1 Basic configuration of variable frequency drive
Each part of a variable frequency drive has the following function.
Converter: Circuit to change the commercial AC power supply to the DC
Smoothing circuit: Circuit to smooth the pulsation included in the DC
Inverter: Circuit to change the DC to the AC with variable frequency
Control circuit: Circuit to mainly control the inverter part
Before you attempt to dissipate causative factors of harmonics verbally, you take a look at several studies done by NEMA regarding such, and look into variable frequency drive (VFD) a bit better. You can view articles and studies by subscribing to the NEMA newsletter, and find other sources quite readily through NEMA. It's an easily accessible place for many current dissertations on this and other electrical topics, with excellent subject matter.
Categorizing all VFDs into the same bucket doesn't get it. You can also look at EPRI reports done better than 15 years ago on this and other VFD oriented subjects. Of course, all VFDs use Pulse Width Modulation to create the AC type wave form output (AKA 'Sinusoidal Flows) and of course all have rectifiers at the top end, as do all computers, PLCs, and many solid state control components. The differences of transient creation on the outputs of variable frequency drives depend upon the quality of the wave form output. The more transients or 'spikes' in the wave form, the more disruption potential. The quality of outputs of variable frequency drives can clearly be seen in testing with oscilloscopes. Several VFDs on the market significantly reduce this effect with chokes up front, and on the output. It really is a garbage in/garbage out situation that lesser drives don't bother to address.
Categorizing all VFDs into the same bucket doesn't get it. You can also look at EPRI reports done better than 15 years ago on this and other VFD oriented subjects. Of course, all VFDs use Pulse Width Modulation to create the AC type wave form output (AKA 'Sinusoidal Flows) and of course all have rectifiers at the top end, as do all computers, PLCs, and many solid state control components. The differences of transient creation on the outputs of variable frequency drives depend upon the quality of the wave form output. The more transients or 'spikes' in the wave form, the more disruption potential. The quality of outputs of variable frequency drives can clearly be seen in testing with oscilloscopes. Several VFDs on the market significantly reduce this effect with chokes up front, and on the output. It really is a garbage in/garbage out situation that lesser drives don't bother to address.
The potential for variable frequency drive (VFD) energy saving from slowing down the load depend on the characteristics of the load being driven. There are three main types of load: variable torque, constant torque and constant power.
Variable torque loads are typical of centrifugal fans and pumps and have the largest energy saving potential controlled by variable frequency drives. They are governed by the Affinity Laws which describe the relationship between the speed and other variables.
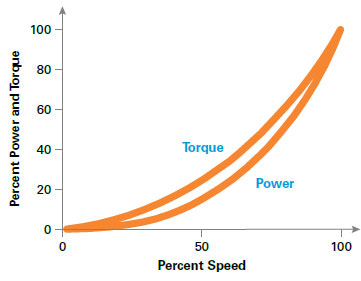
Variable torque loads are typical of centrifugal fans and pumps and have the largest energy saving potential controlled by variable frequency drives. They are governed by the Affinity Laws which describe the relationship between the speed and other variables.
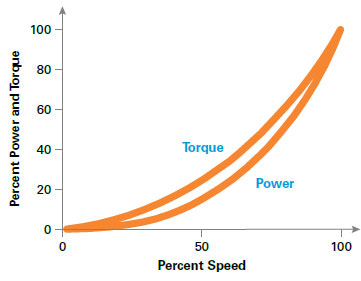
The rotating electrical machines have basically three noise sources:
In motors fed by sinusoidal supply, especially those with reduced pole numbers (higher speeds), the main source of noise is the ventilation system. On the other hand, in motors of higher polarities and lower operation speeds often stands out the electromagnetic noise.
However, in variable frequency drive (VFD) systems, especially at low operating speeds when ventilation is reduced, the electromagnetically excited noise can be the main source of noise whatever the motor polarity, owing to the harmonic content of the voltage.
- The ventilation system
- The rolling bearings
- Electromagnetic excitation
In motors fed by sinusoidal supply, especially those with reduced pole numbers (higher speeds), the main source of noise is the ventilation system. On the other hand, in motors of higher polarities and lower operation speeds often stands out the electromagnetic noise.
However, in variable frequency drive (VFD) systems, especially at low operating speeds when ventilation is reduced, the electromagnetically excited noise can be the main source of noise whatever the motor polarity, owing to the harmonic content of the voltage.
For the AC power line, the system (VFD + motor) is a non-linear load whose current include harmonics (frequency components multiples of the power line frequency). The characteristic harmonics generally produced by the rectifier are considered to be of order h = np±1 on the AC side, that is, on the power line (p is the number of pulses of the variable frequency drive and n =1,2,3).
Thus, in the case of a 6 diode (6 pulses) bridge, the most pronounced generated harmonics are the 5th and the 7th ones, whose magnitudes may vary from 10% to 40% of the fundamental component, depending on the power line impedance. In the case of rectifying bridges of 12 pulses (12 diodes), the most harmful harmonics generated are the 11th and the 13th ones. The higher the order of the harmonic, the lower can be considered its magnitude, so higher order harmonics can be filtered more easily. As the majority of VFD manufacturers, Gozuk produces its low voltage standard variable frequency drives with 6-pulse rectifiers.
Harmonic currents, which circulate through the power line impedances and depend on the rectifier input/output impedance values, cause harmonic voltage drops that distort the power supply voltage of the variable frequency drive and other loads connected to this line. These harmonic current and voltage distortions may increase the electrical losses in the installation, lowering the power factor and overheating components such as cables, transformers, capacitor banks, motors, etc.
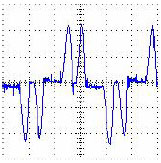
Harmonic currents, which circulate through the power line impedances and depend on the rectifier input/output impedance values, cause harmonic voltage drops that distort the power supply voltage of the variable frequency drive and other loads connected to this line. These harmonic current and voltage distortions may increase the electrical losses in the installation, lowering the power factor and overheating components such as cables, transformers, capacitor banks, motors, etc.
Investing in energy efficient variable frequency drives (VFD) seems like an obvious path to cutting a company's operating
costs, but it is one that many companies ignore. This article explores
some possible reasons for this reluctance to invest in VFD.
There is a goldmine of savings waiting to be unlocked by controlling electric motors, but the reluctance to take advantage of this is a very puzzling phenomenon. Motors consume about two thirds of all electrical energy used by industry and cost 40 times more to run than to buy, so you would think optimizing their efficiency would be a priority. The reality is that this good idea is not always turned into good practice and many businesses are missing out on one of the best opportunities to boost profits and variable frequency drive growth.
There is a goldmine of savings waiting to be unlocked by controlling electric motors, but the reluctance to take advantage of this is a very puzzling phenomenon. Motors consume about two thirds of all electrical energy used by industry and cost 40 times more to run than to buy, so you would think optimizing their efficiency would be a priority. The reality is that this good idea is not always turned into good practice and many businesses are missing out on one of the best opportunities to boost profits and variable frequency drive growth.
The key to optimizing the system operation is communication and information sharing through the entire system equipment. With the reduced cost of variable frequency drives and Building Automation Systems, (BAS) complete system optimization can be implemented as a cost effective option.
Modulating Supply & Return Fans are used as a means of providing proper variable air volume (VAV) control as well as building pressurization. Many such VAV systems are still largely pneumatic with static to the downstream boxes being maintained by inlet guide vanes. To provide increased energy savings and energy comfort, these systems can be easily converted to frequency inverter fan control of the supply and return fans and Direct Digital Control (DDC) to coordinate any increased energy saving strategies.
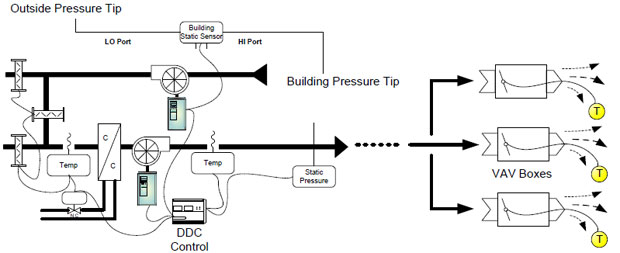
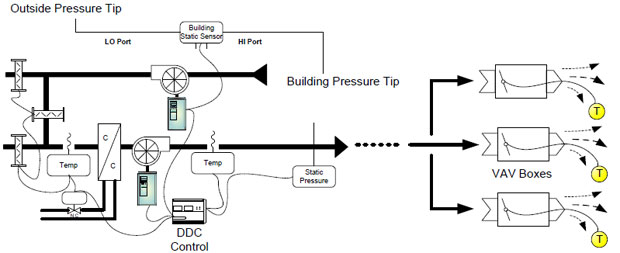
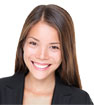
Featured
Like pumps, fans consume significant electrical energy while serving several applications. In many plants, the VFDs (variable ...
A frequency inverter controls AC motor speed. The frequency inverter converts the fixed supply frequency (60 Hz) to a ...
Motor starter (also known as soft starter, motor soft starter) is a electronic device integrates soft start, soft stop, ...
Soft starter allows the output voltage decreases gradually to achieve soft stop, in order to protect the equipment. Such as the ...
Soft Starter reduces electric motor starting current to 2-4 times during motor start up, reduces the impact to power grid during ...

In Discussion
VFD DBR and Active front end
What packaging is used to ship PV panels to their installation location?
One stage 130 meter head pump
What is the role of VARS in system voltage improvement?
how to do load (torque) sharing with Allen Bradley servos?
Is there a high reliability long life energy storing core?
MAXIMUM POWER TRANSFER during Grid Synchronization
A need of change in Solar technology in Rajasthan
What packaging is used to ship PV panels to their installation location?
One stage 130 meter head pump
What is the role of VARS in system voltage improvement?
how to do load (torque) sharing with Allen Bradley servos?
Is there a high reliability long life energy storing core?
MAXIMUM POWER TRANSFER during Grid Synchronization
A need of change in Solar technology in Rajasthan