The rotating electrical machines have basically three noise sources:
In motors fed by sinusoidal supply, especially those with reduced pole numbers (higher speeds), the main source of noise is the ventilation system. On the other hand, in motors of higher polarities and lower operation speeds often stands out the electromagnetic noise.
However, in variable frequency drive (VFD) systems, especially at low operating speeds when ventilation is reduced, the electromagnetically excited noise can be the main source of noise whatever the motor polarity, owing to the harmonic content of the voltage.
- The ventilation system
- The rolling bearings
- Electromagnetic excitation
In motors fed by sinusoidal supply, especially those with reduced pole numbers (higher speeds), the main source of noise is the ventilation system. On the other hand, in motors of higher polarities and lower operation speeds often stands out the electromagnetic noise.
However, in variable frequency drive (VFD) systems, especially at low operating speeds when ventilation is reduced, the electromagnetically excited noise can be the main source of noise whatever the motor polarity, owing to the harmonic content of the voltage.
When I was doing my PhD in motor design of reluctance machines with flux assistance (switched reluctance machines and flux switching machines with magnets and/or permanently energised coils) my supervisor was doing research on the field of sensorless control (it wasn't the area of my research but it got me thinking about it all).
You can build it all in MagNet using the circuit position controlled switch. You will have to use motion analysis in order to use the position controlled switches. You can also use the back EMF information to find what the optimal position for the rotor should be with respect to the stator field. The nice thing about motion is that even if you do not have the rotor in the proper position you can set the reference at start up.
Large machines are - generally speaking - made of pieces (segments) because the circle for the stator and/or rotor core is too large to manufacture from a single sheet. This leads to some breaks in the magnetic flux path symmetry, both in the radial (right angles to the shaft) and axial (parallel to the shaft) directions.
As using soft starter could result in reducing torque of the motor. Soft starter normally reduces starting current by reducing starting voltage. However, decreasing voltage will lead to starting toque reduction. Hence, the motor may take longer time, especially when driving high-inertia load, with somewhat high current until it reach its full speed. Using an inverter will help you get full starting torque or even boost up it to 150-200% while keeping starting current at 150-200% of full load. Installation of heat tracing might also help and economic.
It is not easily answered since there are many variables at play which will affect the starting time. For a large medium voltage motor, it is recommended that a motor starting analysis be performed so that proper control and protection of the motor can be set. The motor manufacturer is a good place to start to find a motor data sheet and torque curve responses; that should give you some good starting point data. Such an analysis can provide inrush current, voltage dip, and starting time.
First, you need to know power (rated power and rated current) of your power source with whom you will supply your motor. For example, if you want to supply your motor by using low voltage synchronous generator (through high voltage power transformer), you need to know rated power and rated current of synchronous generator and rated power and rated currents of high voltage power transformer.
Can an AC drive to replace the mechanical gearbox that used to decrease motor speed in conveyor application i.e to use a motor that will drive the load directly throw a coupling, belt or chain, without gearbox, motor rated up to 18.5 kw.
In motor protection panel when 3 fuses are provided for short circuit protection, Is it always a condition that during short circuit minimum 2 fuses should be blown? If yes or no then why?
Its essential component is a metal wire or strip that melts when too much current flows, which interrupts the circuit in which it is connected.
Its essential component is a metal wire or strip that melts when too much current flows, which interrupts the circuit in which it is connected.
An AC induction motor is supposed to be a constant power motor, which implies it draws more current on low voltage. Consider a motor running a constant torque load at a particular speed. Suppose now the voltage is reduced, which should cause it to settle down at a lower speed supplying the same torque as per the new torque speed characteristic.
Many years ago I had an experience of 4nos 37kW fin-fan motors wrongly connected at site to a star. After running for almost 1 year, the operators reported these motors were very warm and felt unusual. We removed one of them to the workshop and opened for inspection. All windings were OK but the rotor lamination surface had turned to light blue colour which showed a sign of abnormal heating.
Variable speed drive switches very fast which brings high dv/dt on motor. How often do we face with problems coming with VSD? How harmful is the common mode currents in windings and other parts of motor due to high dv/dt. Do we see winding isolation failure? How much does the life of motor reduce? Also, is the filtering of voltage at the output of inverter common or applicable practice in the field?
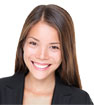
Featured
Like pumps, fans consume significant electrical energy while serving several applications. In many plants, the VFDs (variable ...
A frequency inverter controls AC motor speed. The frequency inverter converts the fixed supply frequency (60 Hz) to a ...
Motor starter (also known as soft starter, motor soft starter) is a electronic device integrates soft start, soft stop, ...
Soft starter allows the output voltage decreases gradually to achieve soft stop, in order to protect the equipment. Such as the ...
Soft Starter reduces electric motor starting current to 2-4 times during motor start up, reduces the impact to power grid during ...

In Discussion
Sensing circuits (Voltage and Current) for Three Phase Inverter
Automated Coil Winding Machines
Could indoor photovoltaics replace batteries?
Suction Pressure and How it varies from Pumps to Pumps
Remote Client function support with the QNX operating system?
Real-time process signature analysis/alarming
What is batter option Chemical Earthing or Traditional Earthing system
The basic test equipment list of the power engineer?
Automated Coil Winding Machines
Could indoor photovoltaics replace batteries?
Suction Pressure and How it varies from Pumps to Pumps
Remote Client function support with the QNX operating system?
Real-time process signature analysis/alarming
What is batter option Chemical Earthing or Traditional Earthing system
The basic test equipment list of the power engineer?