Home » Blog » Motor controls » Page 2
If referring to the acoustic noise generated at or around the PWM frequency of the inverter, then you may notice a very slight difference between "BLDC" and an induction motor. Assume that it's referring to a surface permanent magnet machine for the BLDC and a squirrel cage induction machine. The SPM machine has laminations in the stator that will generate audible noise at a frequency consistent with the inverter's PWM frequency.
There are hundreds of applications for a frequency inverter. I use them on a pump to test pumps with voltages from 208-600VAC 3PH 50 and 60 HZ. You just have to size the frequency inverter to the largest 208 HP motor, so it can handle the current. Many people are installing them on pumps, fans and air compressors to get the energy savings of lowering the speed on the motor to maintain the pressure, temperature and flow.
At zero speed the motor requires torque which is flux (voltage) and current (mostly reactive). Only a little bit of active current to compensate for the motor power losses.
Only the power losses need to be drawn from the grid at that time, which means a very small amount of current. It may produce 200% current on the motor and pull only 10% current from the grid.
Only the power losses need to be drawn from the grid at that time, which means a very small amount of current. It may produce 200% current on the motor and pull only 10% current from the grid.
Its beneficial to opt for the AC Drives as it supports SLVC [ VFD gives almost servo-like torque at low rpms if you give it encoder feedback ], multiple motors can be accessed, torque requirement can be met if required, power dips can be sustained using VFD's.
When a choosing a power cable for a motor, we prefer using one larger diameter cable than two smaller diameter cables in parallel, although it would cost less to do so. Why?
Generally, electric motors are designed according to 50Hz power supply, its rated torque also in this frequency. Therefore, the speed adjustment under rated frequency called constant torque speed adjustment. (T = Te, P <= Pe).
If the variable speed drive outputs frequency exceeds 50Hz, the motor torque is inversely proportional to the frequency in linear relationship decrease. When the motor running in above 50Hz frequency, we should consider the motor loads to avoid motor lacks of torque.
If the variable speed drive outputs frequency exceeds 50Hz, the motor torque is inversely proportional to the frequency in linear relationship decrease. When the motor running in above 50Hz frequency, we should consider the motor loads to avoid motor lacks of torque.
As you know the inductance of SRM depends on two parameters: 1.coil current 2.rotor position .it means that you have a lot of possible situation that each situation has particular value of inductance .if you want to measure inductance at particular position, I think you should excite one phase with ac supply and use circuit equations (kvl) to find inductance. if you use a dc supply you should measure the flux and it's hard to do.
The method of creating a die-cast rotor is as follows:
1. An assembly of steel laminations (which may or may not be grain-oriented) containing the openings for both rotor bars and ventilation (as required) is made and clamped together to form a cylindrical iron core.
2. The assembly is inserted into a mold, which has space both above and below the core for the end (shorting) ring assembly.
1. An assembly of steel laminations (which may or may not be grain-oriented) containing the openings for both rotor bars and ventilation (as required) is made and clamped together to form a cylindrical iron core.
2. The assembly is inserted into a mold, which has space both above and below the core for the end (shorting) ring assembly.
Overload protection: the soft starter has current control loop to track and detect of the changes of the electric motor current. Achieve overload protection by increasing overload current settings and inverse time control mode, to cut down the thyristor and send alarm signals when motor is overload.
Koil can make the synthesis (i.e. design the winding layout from slot-pole combination) only for symmetrical windings. To have a symmetrical 3-phase winding the back EMFs must be equal and out of phase of 120 electrical degrees. Looking at the star of slots, this means that the spokes in the star (or phasors, one for each slot) must be equally spaced and the number of spokes must be multiple of the phase number.
SCR's are limited to a maximum current rating, as well as a maximum voltage rating. In addition, the number of starts per hour is also limited. A combination of voltage spikes, too many starts per hour, or too much current during a start will destroy a soft starter. Phase imbalance for either voltage or current will cause an SCR to fail, as will a single phase condition on a 3-phase motor. What also needs to be considered is the load being started. If it is a high starting torque load it may require a heavy duty version of soft starter to get it going.
We also recommend looking for faults conducive to stator failures. For example, if you have a high restive imbalance on the circuit this can increase heat inside the motor. The increased heat further stresses the insulation system and can lead to bigger insulation or stator failures. If we could have found the small problem, ie. resistance imbalance, then we could have prevented the stator fault.
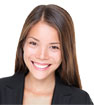
Featured
Like pumps, fans consume significant electrical energy while serving several applications. In many plants, the VFDs (variable ...
A frequency inverter controls AC motor speed. The frequency inverter converts the fixed supply frequency (60 Hz) to a ...
Motor starter (also known as soft starter, motor soft starter) is a electronic device integrates soft start, soft stop, ...
Soft starter allows the output voltage decreases gradually to achieve soft stop, in order to protect the equipment. Such as the ...
Soft Starter reduces electric motor starting current to 2-4 times during motor start up, reduces the impact to power grid during ...

In Discussion
AODD To Electric Driven Pump
ICAPS simulator question
Which types of pumps are used in chilled water systems?
Microlense coated PV panels compared to traditional flat surface panels
transformer back charging
How much will the solar panel will cost and its production capacity
High efficiency DC-DC converter - Topology recommendation
Over voltage and under voltage protection for line fed equipments
ICAPS simulator question
Which types of pumps are used in chilled water systems?
Microlense coated PV panels compared to traditional flat surface panels
transformer back charging
How much will the solar panel will cost and its production capacity
High efficiency DC-DC converter - Topology recommendation
Over voltage and under voltage protection for line fed equipments