The baseline figure should be obtained from either factory or during initial commissioning (as per factory condition). So performing commissioning in the rain, dirty surface, high humidity may result in low values for both dry type and oil filled equipment. Low reading in itself does not indicate bad insulation where the machine cannot be returned to service.
The excitation system requires a very small fraction of the total power being generated. If we could simply increase the excitation (a very small amount of power) and increase the generator's real power output, the world's energy problems would be solved, because we would have a perpetual motion machine.
Phase rotation errors are not as rare as they ought to be. I've seen more than one building with a systematic phase rotation error. This can be prevented by carefully following the color coding system (Yellow Orange Brown and Red Blue Black for 480 volt and 208 volt systems in the US for example) and tagging feeders at both ends to assure proper connections.
The first question would have to be - why do want to do it? If the data already exists in one location that is accessible by all parts of the program, why are you going to use up more PLC memory with exactly the same data?
Since one end is tied together and the two other ends are from different substations, then you will have the classic voltage sending and receiving formula. Since the load is the one substation, then their will only be one power factor of the one load, so I would think this formula would apply: Es = Square Root of ((ErCosƟ + IR)² +(ErSinƟ +IX)²), which is square root of ((Receiving voltage times the cosine of the current phase angle plus current times resistance of the line)² + (Receiving voltage times Sine of the current phase angle plus current times reactance of the line)²).
Usually in your case there should be Electrical as well as Mechanical interlocks between the mains incomer & genset main breaker. ie both Sources will never be in Synchronism ( will not feeding the same load simultaneously).This measures will ensure that there will be only neutral point to the system.
As using soft starter could result in reducing torque of the motor. Soft starter normally reduces starting current by reducing starting voltage. However, decreasing voltage will lead to starting toque reduction. Hence, the motor may take longer time, especially when driving high-inertia load, with somewhat high current until it reach its full speed. Using an inverter will help you get full starting torque or even boost up it to 150-200% while keeping starting current at 150-200% of full load. Installation of heat tracing might also help and economic.
If you are using soft starters now, do not take them out. These are really large motors and starting them across the line is not a good idea. The utility serving you should have designed their service based on you having soft starters for these motors. They probably also have a stipulation stating that you cannot start them all at the same time. Starting one or more them across the line may cause the utility's transformer fuses to fail.
Make sure your generator can start your largest motor and that your disconnect breaker or fuses can handle the inrush. I have seen this as an issue, especially when soft starters are used. Soft starters lower the inrush by exploiting the time characteristic. If the soft starter settings do not bring the motor up to speed quickly enough, the overload trip setting on your generator may trip.
Most electric motors that suffer variations in Load already have variable frequency drives, we have capacitors installed in general switchboard to correct the reactive energy and so on. I did a discretization of the electrical consumption by product type, during this energy survey I noticed that in most motors Amperage THD was high, above 40%. I would like to know what effect does it have on efficiency and possible causes and solutions.
Soft Start and Soft Stop is especially useful with pumping fluids where torque transients often cause water hammer effects, and in some instances, failure to gradually slow the fluid down before stopping, can cause the kinetic energy to rupture pipes and couplings.
It is not easily answered since there are many variables at play which will affect the starting time. For a large medium voltage motor, it is recommended that a motor starting analysis be performed so that proper control and protection of the motor can be set. The motor manufacturer is a good place to start to find a motor data sheet and torque curve responses; that should give you some good starting point data. Such an analysis can provide inrush current, voltage dip, and starting time.
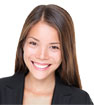
Featured
Like pumps, fans consume significant electrical energy while serving several applications. In many plants, the VFDs (variable ...
A frequency inverter controls AC motor speed. The frequency inverter converts the fixed supply frequency (60 Hz) to a ...
Motor starter (also known as soft starter, motor soft starter) is a electronic device integrates soft start, soft stop, ...
Soft starter allows the output voltage decreases gradually to achieve soft stop, in order to protect the equipment. Such as the ...
Soft Starter reduces electric motor starting current to 2-4 times during motor start up, reduces the impact to power grid during ...

In Discussion
Rated and Normal pump flow
solar cell to module conversion loss
Controlling exotherm in a batch reactor using cooling water
What are 3 of the biggest risks when investing in PV energy?
PLCs vs. RTUs -- What's the difference?
In case Copper, annealed soft-drawn...
Solar PV Farms 1 MW to 50 MW - Investment Capital
400 kV transmission line charging
solar cell to module conversion loss
Controlling exotherm in a batch reactor using cooling water
What are 3 of the biggest risks when investing in PV energy?
PLCs vs. RTUs -- What's the difference?
In case Copper, annealed soft-drawn...
Solar PV Farms 1 MW to 50 MW - Investment Capital
400 kV transmission line charging