The guy asked for suggestions on how to improve troubleshooting techniques. I mentioned this earlier as a "suggestion" for starters but the idea got lost in all the complaining and totally irrelevant responses like the one above.
Ahh I see the words machine tool and shop floor; now I can see where you guys are coming from. The type of machines that you talk about were controlled by relay logic and then when technology arrived the electrical drawings were probably "converted" into ladder logic. The techs had lots to do because you cannot translate relay based systems into ladder logic 100% successfully as they behave differently.
The biggest differences between the floor programmer and the office programmer is often a piece of paper (knowledge and experience do not replace a piece of paper in the mind of HR person that has no understanding of the position they are seeking to fill) and that the floor programmer must produce a working machine.
If I had a "critical" operation with a double-action cylinder, hydraulic or pneumatic, I'd put proximity sensors on both ends of travel, typically with small metal "marker" on the shaft. Each input "in series" with the "output” to each coil, time delayed to give the cylinder a chance to reach its destination. The "timer" feeds the "alarm." If you want to spend the money for a pressure switch (or transducer) on each solenoid output, that's a plus.
The owner of the system should provide clear requirements of what the system should do and should define what constitutes "maintainability" of the system. This places a burden on the owner of the system to consider the full life-cycle of the system.
Even the humble motor car runs diagnostics that the garage read to see the problems with your car. This doesn't involve technicians looking at the code that controls the car but is 100% driven by the faults flagged by the car's management system programs. These could even be displayed to the users, the drivers like me and you but the manufacturers don't want amateurs hacking around their management systems and you know that is exactly what we would do.
In many instances, the result of step 4 (Requirements Analysis), is an RFQ for the system implementation has been issued to one or more systems integrators. Upon selecting the system integrator, step 5 (Design) begins. Upon completing step 5 (Design), the system or process flow is defined. One of the major outputs from step 5 are the RFQs for the major functional components of the finished system. Based on the RFQ responses (bids), the Machine or device manufacturers are chosen.
Many of the techniques contributed by others in the discussion address faults, but how do you address the "normal" things that can hold up an action such as waiting for a process condition to occur, such as waiting for a level/pressure/temperature to rise above/fall below a threshold or waiting for a part to reach a limit switch?
How to make our systems so friendly that they do not need technicians to help diagnose problems? Most of the more obvious answers have been well documented here but to emphasize these points it is normally the case that diagnostics and alarms can dominate the amount of code constructed for an application.
The industry as a whole needs to enforce better system design and performance. This initiative will come from the clients, and implemented by the developers. The cost/benefit trade-off will always be present. Developers trying to improve their margins (reduce cost - raise price) and customers raising functionality and willing to pay less. "We as engineers" are caught in the middle, trying to find better ways to achieve the seemingly impossible.
KW is true power and KVA is apparent power. In per unit calculations the more predominantly used base, which I consider standard is the KVA, the apparent power because the magnitude of the real power (KW) is variable / dependent on a changing parameter of the cos of the angle of displacement (power factor) between the voltage and current. Also significant consideration is that the rating of transformers are based in KVA, the short circuit magnitudes are expressed in KVA or MVA, and the short circuit duty of equipment are also expressed in MVA (and thousands of amperes, KA ).
I once uprated a set of 3x 500KVA 11/.433kv ONAN transformers to 800KVA simply by fitting bigger radiators. This was with the manufacturers blessing. (not hermetically sealed - there were significant logistical difficulties in changing the transformers, so this was an easy option). Limiting factor was not the cooling but the magnetic saturation of the core at the higher rating. All the comments about uprating the associated equipment are relevant, particularly on the LV side.
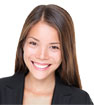
Featured
Like pumps, fans consume significant electrical energy while serving several applications. In many plants, the VFDs (variable ...
A frequency inverter controls AC motor speed. The frequency inverter converts the fixed supply frequency (60 Hz) to a ...
Motor starter (also known as soft starter, motor soft starter) is a electronic device integrates soft start, soft stop, ...
Soft starter allows the output voltage decreases gradually to achieve soft stop, in order to protect the equipment. Such as the ...
Soft Starter reduces electric motor starting current to 2-4 times during motor start up, reduces the impact to power grid during ...

In Discussion
Transient Stability study
Thesis Project in Electrical Engineering
Phase shifted full bridge converter primary current ringing
What is the earthed & unearthed system?
Voltage Multiplier Boost Converter
Anti-parallel diode in resonant power supplies
Can my EMC receiver be missing signals??
Disadvantage of connecting a metering relay in series with protection relay in one CT core
Thesis Project in Electrical Engineering
Phase shifted full bridge converter primary current ringing
What is the earthed & unearthed system?
Voltage Multiplier Boost Converter
Anti-parallel diode in resonant power supplies
Can my EMC receiver be missing signals??
Disadvantage of connecting a metering relay in series with protection relay in one CT core