DC drives vary the speed of DC motors with greater efficiency & speed regulation than resistor control circuits. Since the speed of a DC motor is directly proportional to armature voltage & inversely proportional to field current, either armature voltage or field current can be used to control speed. To change the direction of rotation of a DC motor, either the armature polarity can be reversed, or the field polarity can be reversed.
A frequency inverter controls AC motor speed. The frequency inverter converts the fixed supply frequency (60 Hz) to a variable-frequency, variable-voltage output to enable precise motor speed control. Many frequency inverters even have the potential to return energy to the power grid through their regenerative capability.


Non-regenerative DC drives, also known as single-quadrant drives, rotate in one direction only & they have no inherent braking capabilities. Stopping the motor is done by removing voltage & allowing the motor to coast to a stop. Typically nonregenerative drives operate high friction loads such as mixers, where the load exerts a strong natural brake. In applications where supplemental quick braking and/or motor reversing is required, dynamic braking & forward & reverse circuitry, may be provided by external means.
DC drive technology is the oldest form of electrical speed control. The
speed of a DC motor is the simplest to control, & it can be varied
over a very wide range. These drives are designed to handle applications
such as:
Winders/coilers - In motor winder operations, maintaining tension is very important. DC motors are able to operate at rated current over a wide speed range, including low speeds.
Winders/coilers - In motor winder operations, maintaining tension is very important. DC motors are able to operate at rated current over a wide speed range, including low speeds.
1. List three types of operations where DC drives are commonly found.
2. How can the speed of a DC motor be varied?
3. What are the two main functions of the SCR semi conductors used in a DC drive power converter?
4. Explain how SCR phase angle control operates to vary the DC output from an SCR.
5. Armature-voltage-controlled DC drives are classified as constant-torque drives. What does this mean?
6. Why is three-phase AC power, rather than single phase, used to power most commercial & industrial DC drives?
2. How can the speed of a DC motor be varied?
3. What are the two main functions of the SCR semi conductors used in a DC drive power converter?
4. Explain how SCR phase angle control operates to vary the DC output from an SCR.
5. Armature-voltage-controlled DC drives are classified as constant-torque drives. What does this mean?
6. Why is three-phase AC power, rather than single phase, used to power most commercial & industrial DC drives?
Where we really need digital communication networking, in my personal opinion, is down at the sensor/transmitter and positioner/actuator/valve level to take the place of 4-20 mA and on/off signals. Down at the level 1 of the Purdue reference model you need a fieldbus, not one of the "H2" types of fieldbus, but one of the "H1" types of fieldbus. When first introduced, these technologies were not as fast and not as easy to use has they could have been, but after many years of refinement these technologies are finally becoming sufficiently easy for most plants to use.
First, specify that this is an isolated system with two generators feeding the same bus. Operation of an isolated system is different than a grid connected system, and the mode setting of the governors have to be set to accommodate this. Depending upon the prime mover type and governor model, improper tuning will manifest itself in speed variations. The size of the two machines relative to each other, as well as their size relative to the load, can have measurable impact as well.
The power industry has many tentacles. Energy production is one key subset, the design, manufacture, installation and operation of hydro, nuclear, fossil, renewables, etc is continuing to grow especially in the renewable area.
The UPS systems commissioning test and inspection procedures are to conform to;
• BS EN 50091-1:1993 - Specification for Uninterruptible Power Supplies (UPS). General and Safety Requirements, AND
• IEC 62040-3 (Draft Edition – 2) in particular the Efficiency test procedures outlined in its "Annexure-J".
I have contracted with lots of different groups and moving within the same company to save failed projects or project in trouble or impossible to implement and helped these groups to achieve company goal. What I have noticed is that less the managers or groups know less they realize more knowledge or experience can help them. Less they know, less they understand they need help because they don't know what they need. They think they are just fine until it is too late and a group or company goes under because of it.
Many years ago we used to call this the "what ifs?". Part of the design phase is when we model what we think the system is meant to do. Just as important is how the system is meant to react when things are not going well, the abnormal situations or what ifs?
Panel operator experienced some problems with valve 1 (gas entry) in vessel 2 because it should open but immediately it received the close command. Instruments technician check that orders coming from the DCS were OK, and also check the valves by injecting the open order, so, they and operation staff concluded that "the program has some kind of problem".
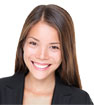
Featured
Like pumps, fans consume significant electrical energy while serving several applications. In many plants, the VFDs (variable ...
A frequency inverter controls AC motor speed. The frequency inverter converts the fixed supply frequency (60 Hz) to a ...
Motor starter (also known as soft starter, motor soft starter) is a electronic device integrates soft start, soft stop, ...
Soft starter allows the output voltage decreases gradually to achieve soft stop, in order to protect the equipment. Such as the ...
Soft Starter reduces electric motor starting current to 2-4 times during motor start up, reduces the impact to power grid during ...

In Discussion
Variable frequency power drive simulator tester
Need Solar Inverters
Cascading SMPSs - be careful of your feedback loops
Why we connect Earth lead with metal tape shield in the cable?
Charging 12V lead-acid battery and PFC converters
distribution T/F of 500kva (delta-Wye) connection
Different of short circuit current 20 kA/3s and 12,5kA/1s
How to select input capacitor for Phase shift controlled full bridge converter
Need Solar Inverters
Cascading SMPSs - be careful of your feedback loops
Why we connect Earth lead with metal tape shield in the cable?
Charging 12V lead-acid battery and PFC converters
distribution T/F of 500kva (delta-Wye) connection
Different of short circuit current 20 kA/3s and 12,5kA/1s
How to select input capacitor for Phase shift controlled full bridge converter