Home » Blog » Experience » Machine tool
Machine tool
Ahh I see the words machine tool and shop floor; now I can see where you guys are coming from. The type of machines that you talk about were controlled by relay logic and then when technology arrived the electrical drawings were probably "converted" into ladder logic. The techs had lots to do because you cannot translate relay based systems into ladder logic 100% successfully as they behave differently.
The guys doing this work are just that programmers. They are probably NOT software engineers and are closer to the shop floor techs who are fiddling about with your machines.
I can and have designed many control systems for automotive type machines such as hobbing machines, milling and borers. Very easy code to write if you do not translate the relay logic directly but use the existing documentation as a reference. All of the systems that I did work really well. I did some similar type of machines in a pharmaceutical plant but that was after another company was kicked out after failing to make the machines work. I had to redesign the whole control philosophy as the machine tool world methods used were really a bad fit for the intended application.
But that is only one facet of the work that we Industrial Automation Engineers do. I work in many different industries where the demands for quality deigned, controlled and maintained systems is paramount. We go through proper project life cycles and we deal with the project from inception through design, build, test and commissioning. We even do the maintenance of the systems. We do not sit in Ivory Towers but do the work at the customer site no matter where that is on the planet.
Electrical engineers are tasked with doing all things electrical and we are tasked with all things control. Programming, that is writing the actual code is only one part of what we do and not necessarily the most time consuming part.
I am here in Kazakhstan at the sharp end of a multi-billion dollar project a long way from any ivory tower. I fix other engineers software too, why? Because the vendor may use offshore resources to code much of the systems that are installed at site. Kazakhstan has extreme Summers (up to 60degC) and Winters (down to -50degC), most of the people are friendly but English is not so prevalent. A long way from your shop floor environment. Far more dangerous too as the plant processes H2S or will when first Oil & Gas comes onshore.
Here I have supported technicians performing loop checks and other engineers doing logic tests. I can diagnose many loop problems without even looking in the code but just by looking at what is happening. I have found that if a loop doesn't work then the techs approach us first as a one stop shop to give them an answer rather than actually trouble shooting the loop themselves.
I said to you guys before you need to get out and look at other industries and see what is going on in the rest of the world. Much of what I have seen would go a long way to improving your world too! Engineers like myself are far away from the "programmers" you have.
The guys doing this work are just that programmers. They are probably NOT software engineers and are closer to the shop floor techs who are fiddling about with your machines.
I can and have designed many control systems for automotive type machines such as hobbing machines, milling and borers. Very easy code to write if you do not translate the relay logic directly but use the existing documentation as a reference. All of the systems that I did work really well. I did some similar type of machines in a pharmaceutical plant but that was after another company was kicked out after failing to make the machines work. I had to redesign the whole control philosophy as the machine tool world methods used were really a bad fit for the intended application.
But that is only one facet of the work that we Industrial Automation Engineers do. I work in many different industries where the demands for quality deigned, controlled and maintained systems is paramount. We go through proper project life cycles and we deal with the project from inception through design, build, test and commissioning. We even do the maintenance of the systems. We do not sit in Ivory Towers but do the work at the customer site no matter where that is on the planet.
Electrical engineers are tasked with doing all things electrical and we are tasked with all things control. Programming, that is writing the actual code is only one part of what we do and not necessarily the most time consuming part.
I am here in Kazakhstan at the sharp end of a multi-billion dollar project a long way from any ivory tower. I fix other engineers software too, why? Because the vendor may use offshore resources to code much of the systems that are installed at site. Kazakhstan has extreme Summers (up to 60degC) and Winters (down to -50degC), most of the people are friendly but English is not so prevalent. A long way from your shop floor environment. Far more dangerous too as the plant processes H2S or will when first Oil & Gas comes onshore.
Here I have supported technicians performing loop checks and other engineers doing logic tests. I can diagnose many loop problems without even looking in the code but just by looking at what is happening. I have found that if a loop doesn't work then the techs approach us first as a one stop shop to give them an answer rather than actually trouble shooting the loop themselves.
I said to you guys before you need to get out and look at other industries and see what is going on in the rest of the world. Much of what I have seen would go a long way to improving your world too! Engineers like myself are far away from the "programmers" you have.
You may also like:
DC drives vary the speed of DC motors with greater efficiency & speed regulation than resistor control circuits. Since the speed of a DC motor is directly proportional to armature voltage & inversely ...
When I was doing my PhD in motor design of reluctance machines with flux assistance (switched reluctance machines and flux switching machines with magnets and/or permanently energised coils) my supervisor was ...
I never just put power to a first prototype and see what happens. Smoke and loud sounds are the most likely result and then you just know that something was not perfect. So how would you test the next ...
Make sure your generator can start your largest motor and that your disconnect breaker or fuses can handle the inrush. I have seen this as an issue, especially when soft starters are used. Soft starters lower ...
The trend toward lower losses in power converters is not apparent in all of the applications of power converters. It is also not apparent that the power converter solution and its losses for a given market ...
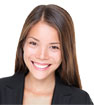
Featured
Like pumps, fans consume significant electrical energy while serving several applications. In many plants, the VFDs (variable ...
A frequency inverter controls AC motor speed. The frequency inverter converts the fixed supply frequency (60 Hz) to a ...
Motor starter (also known as soft starter, motor soft starter) is a electronic device integrates soft start, soft stop, ...
Soft starter allows the output voltage decreases gradually to achieve soft stop, in order to protect the equipment. Such as the ...
Soft Starter reduces electric motor starting current to 2-4 times during motor start up, reduces the impact to power grid during ...

In Discussion
ICAPS simulator question
AODD To Electric Driven Pump
Microlense coated PV panels compared to traditional flat surface panels
Which types of pumps are used in chilled water systems?
High efficiency DC-DC converter - Topology recommendation
Over voltage and under voltage protection for line fed equipments
Is the Automation industry growing?
transformer back charging
AODD To Electric Driven Pump
Microlense coated PV panels compared to traditional flat surface panels
Which types of pumps are used in chilled water systems?
High efficiency DC-DC converter - Topology recommendation
Over voltage and under voltage protection for line fed equipments
Is the Automation industry growing?
transformer back charging