Home » Blog » Experience » "critical" operation with a double-action cylinder, hydraulic or pneumatic
"critical" operation with a double-action cylinder, hydraulic or pneumatic
If I had a "critical" operation with a double-action cylinder, hydraulic or pneumatic, I'd put proximity sensors on both ends of travel, typically with small metal "marker" on the shaft. Each input "in series" with the "output” to each coil, time delayed to give the cylinder a chance to reach its destination. The "timer" feeds the "alarm." If you want to spend the money for a pressure switch (or transducer) on each solenoid output, that's a plus.
Now you can tell if there was an output to the solenoid from internal programming, if not another interlock prevented it from actuating. If there is an output to the solenoid and no pressure, then the signal did not reach the coil (loose wire somewhere), if it did the coil may be bad, if the coil is good and no pressure, the solenoid may be stuck or no pressure to it from another supervised failure or interlock. If there was sufficient pressure and the cylinder travel not reached, then the cylinder is stuck.
As a technician crawling over all kinds of other people's equipment since 1975, I could figure out a lot of this from an old relay logic or TTL control system. A VOM confirms whether there is an output to the correct solenoid at the control panel terminals. This lets you now which direction to head next. If there is no power, it's "upstream" of there, another interlock input that needs to be confirmed, time to dig into the “program.”
If there is power and the cylinder does not move it's a problem outside of those terminals and the control system. I'd remove the wiring and check for coil resistance, confirming the coil and field wiring integrity while still at the panel. If everything checks out then go to the cylinder and see if a pressure gauge shows pressure on the line with the coil energized - presuming there is pressure to the valve. No pressure would be another "input alarm" from another pressure switch. If there is pressure and power to the valve and no pressure, the valve is bad. If there is pressure on the output side and the cylinder does not move - the cylinder is stuck or mechanically overloaded.
I&E "technicians” may know a lot about programming and code, but if they don't know how a piece of equipment operates I/O wise then they don't have a clue where to start looking. Then I guess you need all the sensors and step by step programmed sequences to "spell it out" for them on a screen. A device sequence “flow chart” may help run I/Os out for something like above. I/O status lights on the terminals like PLCs can easily confirm at a glance if you have the proper inputs for a sequence to complete, then you should have the proper outputs. Most output failures are a result of correct missing inputs. The more sensors you’re willing to install, the more the sequence can be monitored and spelled out on an HMI.
From a factory tech support in another location, being able to access the equipment remotely is a huge plus, whether directly through modem, or similar, or indirectly through the local technician's computer to yours i.e. REMOTE ASSISTANCE. A tablet PC is a huge plus with IOMs, schematics and all kinds of info you can hold in one hand while trouble-shooting.
Now you can tell if there was an output to the solenoid from internal programming, if not another interlock prevented it from actuating. If there is an output to the solenoid and no pressure, then the signal did not reach the coil (loose wire somewhere), if it did the coil may be bad, if the coil is good and no pressure, the solenoid may be stuck or no pressure to it from another supervised failure or interlock. If there was sufficient pressure and the cylinder travel not reached, then the cylinder is stuck.
As a technician crawling over all kinds of other people's equipment since 1975, I could figure out a lot of this from an old relay logic or TTL control system. A VOM confirms whether there is an output to the correct solenoid at the control panel terminals. This lets you now which direction to head next. If there is no power, it's "upstream" of there, another interlock input that needs to be confirmed, time to dig into the “program.”
If there is power and the cylinder does not move it's a problem outside of those terminals and the control system. I'd remove the wiring and check for coil resistance, confirming the coil and field wiring integrity while still at the panel. If everything checks out then go to the cylinder and see if a pressure gauge shows pressure on the line with the coil energized - presuming there is pressure to the valve. No pressure would be another "input alarm" from another pressure switch. If there is pressure and power to the valve and no pressure, the valve is bad. If there is pressure on the output side and the cylinder does not move - the cylinder is stuck or mechanically overloaded.
I&E "technicians” may know a lot about programming and code, but if they don't know how a piece of equipment operates I/O wise then they don't have a clue where to start looking. Then I guess you need all the sensors and step by step programmed sequences to "spell it out" for them on a screen. A device sequence “flow chart” may help run I/Os out for something like above. I/O status lights on the terminals like PLCs can easily confirm at a glance if you have the proper inputs for a sequence to complete, then you should have the proper outputs. Most output failures are a result of correct missing inputs. The more sensors you’re willing to install, the more the sequence can be monitored and spelled out on an HMI.
From a factory tech support in another location, being able to access the equipment remotely is a huge plus, whether directly through modem, or similar, or indirectly through the local technician's computer to yours i.e. REMOTE ASSISTANCE. A tablet PC is a huge plus with IOMs, schematics and all kinds of info you can hold in one hand while trouble-shooting.
You may also like:
We have system which is connected to 16kV/2.4 utility transformer (delta on secondary) and we are using 2.kV/480V transformer for loads after 2000ft. Utility wants to protect against ground fault in the ...
Generally, variable frequency drive contains two components: rectifier and inverter. The rectifier converts incoming AC power to DC power, then the inverter converts DC power to the desired frequency AC power. ...
I once uprated a set of 3x 500KVA 11/.433kv ONAN transformers to 800KVA simply by fitting bigger radiators. This was with the manufacturers blessing. (not hermetically sealed - there were significant ...
If there is frequent current-limitation or overcurrent alarm during the variable speed drive running, we should check the loads and inverter IGBT module is normal or not, if its good, then the failure is the ...
In bushing insulation test there are three major current elements which any of those could affect the test result. These current elements are Capacitive current, leakage current and creepage current. In Tan ...
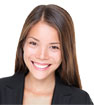
Featured
Like pumps, fans consume significant electrical energy while serving several applications. In many plants, the VFDs (variable ...
A frequency inverter controls AC motor speed. The frequency inverter converts the fixed supply frequency (60 Hz) to a ...
Motor starter (also known as soft starter, motor soft starter) is a electronic device integrates soft start, soft stop, ...
Soft starter allows the output voltage decreases gradually to achieve soft stop, in order to protect the equipment. Such as the ...
Soft Starter reduces electric motor starting current to 2-4 times during motor start up, reduces the impact to power grid during ...

In Discussion
Pumping in salty conditions
Calculating 30min annual maximum demand on the substation transformer.
Feedre protection
"Green Economy" Wind, Solar, Green Building, Geothermal are growing
8 Common SCADA Mistakes: EXPOSED
Use the sea as functional platform for the production of Solar Energy
What is the Difference Between SERVO Drives & VFD?
Looking for a High Starting Torque Micro VFD
Calculating 30min annual maximum demand on the substation transformer.
Feedre protection
"Green Economy" Wind, Solar, Green Building, Geothermal are growing
8 Common SCADA Mistakes: EXPOSED
Use the sea as functional platform for the production of Solar Energy
What is the Difference Between SERVO Drives & VFD?
Looking for a High Starting Torque Micro VFD