Home » Blog » Motor controls » Motor power cable - bigger or smaller?
Motor power cable - bigger or smaller?
When a choosing a power cable for a motor, we prefer using one larger diameter cable than two smaller diameter cables in parallel, although it would cost less to do so. Why?
1. Conductors/Cables/Feeders in parallel connection generally are not recommended unless there is no option, therefore it can be adopted under the following conditions:
i. Cables are of the same material and cross section area.
ii. Are of the same route and length.
iii. The sum of the current carring capacity of the parallel circuits after applying all necessary applicable correction factors should be greater than the nominal regulated current of the protective device.
iv. The current carrying capacity (before derating) shall be not less than 300A (according to the local authority/Service provider requirement/regulation).
v. Capability of addressing the Thermal & electrodynamics constraints in proper way.
2. Some designs call for parallel connection so as to:
i. Overcome the voltage drop.
ii. Avoid the difficulties of installing big size cables (bending, pulling) due corridor limitation,etc.
iii. Meet the Power demand.
iv. Mitigate the cost (Costwise).
3. For electrical Motors, two connections are normally required. One from MDB to Motor CP and other from CP to the Motor.
By virtue of the requirement of Delta/star starter, two cables are required (Mandatory) between CP & motor (one will be dead just after changing to delta connection).
While the connection from the MDB to CP will be one, sized according to the Motor rating.
However, Parallel connection of Feeders need an expert engineer(s) to meet the requirement since Short Circuit fault protection for parallel circuits require further evaluation from the Engineer that the impact of the short circuit current within the parallel section will have severe fault due to fault current path that can occur in addition subtransient contribution of the downstream system.
1. Conductors/Cables/Feeders in parallel connection generally are not recommended unless there is no option, therefore it can be adopted under the following conditions:
i. Cables are of the same material and cross section area.
ii. Are of the same route and length.
iii. The sum of the current carring capacity of the parallel circuits after applying all necessary applicable correction factors should be greater than the nominal regulated current of the protective device.
iv. The current carrying capacity (before derating) shall be not less than 300A (according to the local authority/Service provider requirement/regulation).
v. Capability of addressing the Thermal & electrodynamics constraints in proper way.
2. Some designs call for parallel connection so as to:
i. Overcome the voltage drop.
ii. Avoid the difficulties of installing big size cables (bending, pulling) due corridor limitation,etc.
iii. Meet the Power demand.
iv. Mitigate the cost (Costwise).
3. For electrical Motors, two connections are normally required. One from MDB to Motor CP and other from CP to the Motor.
By virtue of the requirement of Delta/star starter, two cables are required (Mandatory) between CP & motor (one will be dead just after changing to delta connection).
While the connection from the MDB to CP will be one, sized according to the Motor rating.
However, Parallel connection of Feeders need an expert engineer(s) to meet the requirement since Short Circuit fault protection for parallel circuits require further evaluation from the Engineer that the impact of the short circuit current within the parallel section will have severe fault due to fault current path that can occur in addition subtransient contribution of the downstream system.
You may also like:
Making a connection of 3 phase motor the nameplate shows different voltages for delta it is 380-400 volt and 660-690 volt for star, what option should be selected? the supply Line to Line voltage is ...
This is a finite element analysis tool for various applications.
In power we get the voltage (stress) distribution in equipment like cables, bends in cables etc including stator winding of generators.
Phase rotation errors are not as rare as they ought to be. I've seen more than one building with a systematic phase rotation error. This can be prevented by carefully following the color coding system (Yellow ...
The voltage transient which occurs whenever there is a sudden change in current in an inductive device. Inductors resist a sudden current change.
V=L di/dt
In electric motors this occurs at start up when the ...
Well first let get one thing straight for transformers: the higher the line frequency, the lower the core (iron) losses! The core power loss are proportional to kf*B^2 approximately for any machine, dynamic or ...
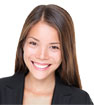
Featured
Like pumps, fans consume significant electrical energy while serving several applications. In many plants, the VFDs (variable ...
A frequency inverter controls AC motor speed. The frequency inverter converts the fixed supply frequency (60 Hz) to a ...
Motor starter (also known as soft starter, motor soft starter) is a electronic device integrates soft start, soft stop, ...
Soft starter allows the output voltage decreases gradually to achieve soft stop, in order to protect the equipment. Such as the ...
Soft Starter reduces electric motor starting current to 2-4 times during motor start up, reduces the impact to power grid during ...

In Discussion
Modbus RS 485 - Daisy Chain Connection
Equipments or instruments used for safety in distillation column?
one cycle control
Do Electric Vehicles Reduce Greenhouse Gas Emissions?
Improvement, technical issues and research areas in power electronics
earthing
Can anybody know how to design a PCB using CNC machine?
can an protection relay system of a switchgear panel be replaced by relay of different make?
Equipments or instruments used for safety in distillation column?
one cycle control
Do Electric Vehicles Reduce Greenhouse Gas Emissions?
Improvement, technical issues and research areas in power electronics
earthing
Can anybody know how to design a PCB using CNC machine?
can an protection relay system of a switchgear panel be replaced by relay of different make?