Home » Blog » Automation controls » Industrial Ethernet vs. Fieldbus technologies
Industrial Ethernet vs. Fieldbus technologies
Where we really need digital communication networking, in my personal opinion, is down at the sensor/transmitter and positioner/actuator/valve level to take the place of 4-20 mA and on/off signals. Down at the level 1 of the Purdue reference model you need a fieldbus, not one of the "H2" types of fieldbus, but one of the "H1" types of fieldbus. When first introduced, these technologies were not as fast and not as easy to use has they could have been, but after many years of refinement these technologies are finally becoming sufficiently easy for most plants to use.
An "H1 fieldbus" is the most practical way to digitally network sensors/transmitters and positioners/actuators/valves to the DCS. Options include FOUNDATION fieldbus H1, PROFIBUS-PA, CompoNet, ASI, and IO-link. These protocols can take the place of 4-20 mA and on/off signals.
Note that "H1 fieldbus" should not be confused with the very different "H2 fieldbus" category of protocols used at level 1-1/2 of the Purdue reference model to connect remote-I/O, PLCs, MCC, variable speed drives, motor starters, and wireless gateways to the DCS;. Options include e.g. DeviceNet, Modbus/RTU, and PROFIBUS-DP. Ethernet is making inroads at level 1-1/2 of the Purdue reference model, where EtherNet/IP, Modbus/TCP, PROFINET are growing as they sometimes are being used in applications which previously used DeviceNet, Modbus/RTU, or PROFIBUS-DP "H2 fieldbus".
Because H1 and H2 are distinctly different in many ways, they should not be lumped together as just "fieldbus". With this in mind it is easy to see that both Ethernet and fieldbus will grow for decades to come
So Ethernet may become a dominant network technology at level 1-1/2 of the Purdue reference model but since Ethernet is not a good fit for level 1 of the Purdue model we don't see Ethernet in sensors and actuators out in the field. For example, pressure, temperature, level, vortex flow, interface level, pH, conductivity, or DO2 transmitter or control valve positioner or on/off valve etc. are not available with Ethernet.
In my personal opinion, the industry can't move forward using 4-20 mA and on/off signals. Modern plants need many more sensors than plants of the past to feed the "big data" paradigm but also for real-time data for equipment reliability, energy conservation, and improved HS&E; maybe 2X or 3X – just like in a modern car vs. a car of the past. Using 4-20 mA and on/off signals for all these sensors is just impractical. We need digital communication from the very "first meter". Just like a modern car has digital communication network for all the sensors (in fact multiple networks for different functions); so should a plant have digital sensor networks too: "H1 fieldbus" as well as wireless sensor networks too.
"H1 fieldbus" will grow and this will generate more data from the sensors/transmitters and positioners/actuators/valves at level 1 of the Purdue reference model which in turn will drive increased use of Ethernet at the higher level networks at level 1-1/2 and above of the Purdue model.
How "H1 fieldbus" complements Ethernet can be seen in how IO-Link was created after PROFINET to support the architecture at level 1 of the Purdue reference model, and how CompoNet was created after EtherNet/IP to support the architecture at level 1 of the Purdue reference model.
An "H1 fieldbus" is the most practical way to digitally network sensors/transmitters and positioners/actuators/valves to the DCS. Options include FOUNDATION fieldbus H1, PROFIBUS-PA, CompoNet, ASI, and IO-link. These protocols can take the place of 4-20 mA and on/off signals.
Note that "H1 fieldbus" should not be confused with the very different "H2 fieldbus" category of protocols used at level 1-1/2 of the Purdue reference model to connect remote-I/O, PLCs, MCC, variable speed drives, motor starters, and wireless gateways to the DCS;. Options include e.g. DeviceNet, Modbus/RTU, and PROFIBUS-DP. Ethernet is making inroads at level 1-1/2 of the Purdue reference model, where EtherNet/IP, Modbus/TCP, PROFINET are growing as they sometimes are being used in applications which previously used DeviceNet, Modbus/RTU, or PROFIBUS-DP "H2 fieldbus".
Because H1 and H2 are distinctly different in many ways, they should not be lumped together as just "fieldbus". With this in mind it is easy to see that both Ethernet and fieldbus will grow for decades to come
So Ethernet may become a dominant network technology at level 1-1/2 of the Purdue reference model but since Ethernet is not a good fit for level 1 of the Purdue model we don't see Ethernet in sensors and actuators out in the field. For example, pressure, temperature, level, vortex flow, interface level, pH, conductivity, or DO2 transmitter or control valve positioner or on/off valve etc. are not available with Ethernet.
In my personal opinion, the industry can't move forward using 4-20 mA and on/off signals. Modern plants need many more sensors than plants of the past to feed the "big data" paradigm but also for real-time data for equipment reliability, energy conservation, and improved HS&E; maybe 2X or 3X – just like in a modern car vs. a car of the past. Using 4-20 mA and on/off signals for all these sensors is just impractical. We need digital communication from the very "first meter". Just like a modern car has digital communication network for all the sensors (in fact multiple networks for different functions); so should a plant have digital sensor networks too: "H1 fieldbus" as well as wireless sensor networks too.
"H1 fieldbus" will grow and this will generate more data from the sensors/transmitters and positioners/actuators/valves at level 1 of the Purdue reference model which in turn will drive increased use of Ethernet at the higher level networks at level 1-1/2 and above of the Purdue model.
How "H1 fieldbus" complements Ethernet can be seen in how IO-Link was created after PROFINET to support the architecture at level 1 of the Purdue reference model, and how CompoNet was created after EtherNet/IP to support the architecture at level 1 of the Purdue reference model.
You may also like:
At zero speed the motor requires torque which is flux (voltage) and current (mostly reactive). Only a little bit of active current to compensate for the motor power losses.
Only the power losses need to be ...
When you want to select current transformer with appropriate rated power for your power system, you need to consider that value of rated power of selected current transformer should be higher from sum of ...
For AM & FM radio & some data communications adding the QP filter make sense.
Now that broadband, wifi, data communications of all sizes & flavours exist - any peak noise is very likely to cause ...
1. How does this affect the vector group (YNd1) of the transformer? Will it be changed to YNd11?
2. Will it make any difference as far as the vector group is concerned if instead of phase A and C, phase B ...
You can calculate current setting of overcurrent relay by using next expression:
Isetting ≥ (ks*Imaxopam)/(a*pi)
Imaxopam=kam*Imaxoptr
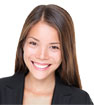
Featured
Like pumps, fans consume significant electrical energy while serving several applications. In many plants, the VFDs (variable ...
A frequency inverter controls AC motor speed. The frequency inverter converts the fixed supply frequency (60 Hz) to a ...
Motor starter (also known as soft starter, motor soft starter) is a electronic device integrates soft start, soft stop, ...
Soft starter allows the output voltage decreases gradually to achieve soft stop, in order to protect the equipment. Such as the ...
Soft Starter reduces electric motor starting current to 2-4 times during motor start up, reduces the impact to power grid during ...

In Discussion
What is relation between frequency and voltage?
Servo system
How to connect CU320-2 PN in Tia Portal V11 SP2.
Active PFC Topology - 115 Vac, 60 Hz input to 90 VDC at 6 Amps (540 Watts) output?
How do you think of PV Power Optimizer?
High Efficiency Converters - Next Generation
how to improve the power factor to unity at 33 kv line?
Can anybody tell me the difference between DCS and PLC's?
Servo system
How to connect CU320-2 PN in Tia Portal V11 SP2.
Active PFC Topology - 115 Vac, 60 Hz input to 90 VDC at 6 Amps (540 Watts) output?
How do you think of PV Power Optimizer?
High Efficiency Converters - Next Generation
how to improve the power factor to unity at 33 kv line?
Can anybody tell me the difference between DCS and PLC's?