Simulation interpretation in automation industry
Related to "automation industry", there are generally 3 different interpretations of what simulations is:
1) Mechanical Simulations – Via various solid modeling tools and cad programs; tooling, moving mechanisms, end-effectors… are designed with 3D visualizations, connecting the modules to prevent interference, check mass before actual machining…
2) Electronics Simulations – This type of simulations are either related to the manufacturers of "specific instrumentations" used in automation industry (ultrasonic welders, laser marking systems,…) or the designers of circuit boards.
3) Electrical & Controls Simulations.
A) Electrical Schematics, from main AC disconnect switch, down to 24VDC low amps for I/O interface.
Simulation tools allow easy determinations of system's required amperage, fuse sizes, wire gauges, accordance with standards (CE, UL, cUL, TUV…)…
B) Logic Simulations, HMI interface, I/O exchange, motion controls…
a) If you want to have any kind of meaningful simulations, get in the habit of "modular ladder logic" circuit design. This means, don't design your ladder like one continuous huge program that runs the whole thing; simulating this type of programs is almost impossible in every case. Break down the logic to sub-systems or maybe even down to stand alone mechanisms (pick & place, motor starter…), simulating and troubleshooting this scenario is fairly easy.
b) When possible, beside automated run mode of the machine or system, build "manual mode logic" for it as well. Then via physical push-buttons or HMI, you should have "step forward" & "step back" for every "physical movement or action".
Simulating the integrity of the "ladder logic program" and all the components and interfaces will be a breeze if things are done meticulously upfront.
1) Mechanical Simulations – Via various solid modeling tools and cad programs; tooling, moving mechanisms, end-effectors… are designed with 3D visualizations, connecting the modules to prevent interference, check mass before actual machining…
2) Electronics Simulations – This type of simulations are either related to the manufacturers of "specific instrumentations" used in automation industry (ultrasonic welders, laser marking systems,…) or the designers of circuit boards.
3) Electrical & Controls Simulations.
A) Electrical Schematics, from main AC disconnect switch, down to 24VDC low amps for I/O interface.
Simulation tools allow easy determinations of system's required amperage, fuse sizes, wire gauges, accordance with standards (CE, UL, cUL, TUV…)…
B) Logic Simulations, HMI interface, I/O exchange, motion controls…
a) If you want to have any kind of meaningful simulations, get in the habit of "modular ladder logic" circuit design. This means, don't design your ladder like one continuous huge program that runs the whole thing; simulating this type of programs is almost impossible in every case. Break down the logic to sub-systems or maybe even down to stand alone mechanisms (pick & place, motor starter…), simulating and troubleshooting this scenario is fairly easy.
b) When possible, beside automated run mode of the machine or system, build "manual mode logic" for it as well. Then via physical push-buttons or HMI, you should have "step forward" & "step back" for every "physical movement or action".
Simulating the integrity of the "ladder logic program" and all the components and interfaces will be a breeze if things are done meticulously upfront.
You may also like:
NGR stands for Neutral Grounding Resistor. When an earth fault current occurs on a plant, assuming that there is no external device presented to limit the earth fault current, the magnitude of the earth fault ...
Even the humble motor car runs diagnostics that the garage read to see the problems with your car. This doesn't involve technicians looking at the code that controls the car but is 100% driven by the faults ...
New improvements make a long list but one of the most recent is being able to switch a DB to and from optimised. How many times in previous versions did I forget to check the box then have to delete the DB and ...
1). Through this policy, it is a Systemic transfer of Public Property to Private Companies, despite failure of many Biomass power projects and Wind mills with a great loss of Tax collection
2). Lot of Debt ...
A completely sensor-less control would be completely open-loop, which isn't reliable with some motors like PMSMs. Even if you knew the switching instants for one ideal case, too many "random" variables could ...
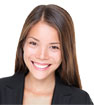
Featured
Like pumps, fans consume significant electrical energy while serving several applications. In many plants, the VFDs (variable ...
A frequency inverter controls AC motor speed. The frequency inverter converts the fixed supply frequency (60 Hz) to a ...
Motor starter (also known as soft starter, motor soft starter) is a electronic device integrates soft start, soft stop, ...
Soft starter allows the output voltage decreases gradually to achieve soft stop, in order to protect the equipment. Such as the ...
Soft Starter reduces electric motor starting current to 2-4 times during motor start up, reduces the impact to power grid during ...

In Discussion
Improve induction motor efficiency
An excellent market for micro-inverters.... Looking for suppliers
vibration frequency analysis
Bode diagram
what is the difference of turbine impellers and propeller agitators?
Progress with solar in India
The basic test equipment list of the power engineer?
Real-time process signature analysis/alarming
An excellent market for micro-inverters.... Looking for suppliers
vibration frequency analysis
Bode diagram
what is the difference of turbine impellers and propeller agitators?
Progress with solar in India
The basic test equipment list of the power engineer?
Real-time process signature analysis/alarming