How to connect 3 phase motor?
Making a connection of 3 phase motor the nameplate shows different voltages for delta it is 380-400 volt and 660-690 volt for star, what option should be selected? the supply Line to Line voltage is 380-400.
Each stator winding of the motor can withstand 380-400 V.
Thus, if you connect your motor (the stator of your motor) in delta, it should be connected to 380-400 V line-to-line.
On the other hand, if you connect the stator winding of your motor in Y, you'd be able to connect your motor to line-to-line voltage that is sqrt(3) x 380-400 V = 660-690 V.
The actual output power (for a standard squirrel cage 3-phase AC motor) is not determined by the motor itself, but by the load it is driving. The motor will attempt to run at a speed near its synchronous speed, and to deliver the power required by the driven machinery at that speed. This means that the current taken up by the motor at any given voltage, will be almost the same whether it is star, or delta connected. If you therefore connect the motor in star while supplying it by the voltage it is designed for when delta connected, the current through each winding will be sqrt(3) times the winding is designed for. This again means that the heat dissipation in the winding will be approximately 3 times what it is designed for, and therefore it will burn out if you load the motor with its nominal load.
We should be aware that the motor power as mentioned on its nameplate, in relation with the available power of the MCC panel to which it is connected, are the important factors in choosing the type of starting of the motor. Take into account the fact that starting the motor direct in Delta connection (which is the correct one based on your network voltage) the currents may be up to 8xInomianl of motor and if your MCC doesn’t have the capacity to withstand this current (by decreasing its supply voltage ) you may fail with DOL Delta starting type. Is that why, based on the power of motors, in order to avoid high currents during the starting time, it is recommended the Y/D connection. Limitations in starting currents by Y/D are considerable by decreasing the current first with sqrt3 because the feeding voltage is not 660V (you feed the motor with 380-400V) and the current initially in Y is sqrt3<I delta, so it is 3 times less than Delta DOL. Y/D is not the single one, there are a lot of solution to start AC motors.
Each stator winding of the motor can withstand 380-400 V.
Thus, if you connect your motor (the stator of your motor) in delta, it should be connected to 380-400 V line-to-line.
On the other hand, if you connect the stator winding of your motor in Y, you'd be able to connect your motor to line-to-line voltage that is sqrt(3) x 380-400 V = 660-690 V.
The actual output power (for a standard squirrel cage 3-phase AC motor) is not determined by the motor itself, but by the load it is driving. The motor will attempt to run at a speed near its synchronous speed, and to deliver the power required by the driven machinery at that speed. This means that the current taken up by the motor at any given voltage, will be almost the same whether it is star, or delta connected. If you therefore connect the motor in star while supplying it by the voltage it is designed for when delta connected, the current through each winding will be sqrt(3) times the winding is designed for. This again means that the heat dissipation in the winding will be approximately 3 times what it is designed for, and therefore it will burn out if you load the motor with its nominal load.
We should be aware that the motor power as mentioned on its nameplate, in relation with the available power of the MCC panel to which it is connected, are the important factors in choosing the type of starting of the motor. Take into account the fact that starting the motor direct in Delta connection (which is the correct one based on your network voltage) the currents may be up to 8xInomianl of motor and if your MCC doesn’t have the capacity to withstand this current (by decreasing its supply voltage ) you may fail with DOL Delta starting type. Is that why, based on the power of motors, in order to avoid high currents during the starting time, it is recommended the Y/D connection. Limitations in starting currents by Y/D are considerable by decreasing the current first with sqrt3 because the feeding voltage is not 660V (you feed the motor with 380-400V) and the current initially in Y is sqrt3<I delta, so it is 3 times less than Delta DOL. Y/D is not the single one, there are a lot of solution to start AC motors.
You may also like:
This is a finite element analysis tool for various applications.
In power we get the voltage (stress) distribution in equipment like cables, bends in cables etc including stator winding of generators.
Phase rotation errors are not as rare as they ought to be. I've seen more than one building with a systematic phase rotation error. This can be prevented by carefully following the color coding system (Yellow ...
When a choosing a power cable for a motor, we prefer using one larger diameter cable than two smaller diameter cables in parallel, although it would cost less to do so. Why?
The voltage transient which occurs whenever there is a sudden change in current in an inductive device. Inductors resist a sudden current change.
V=L di/dt
In electric motors this occurs at start up when the ...
Most electrical steels used in stator and rotor construction also have an insulating coating applied; some of these are organic materials and some are inorganic (solvent-based) materials. The choice is ...
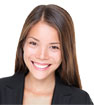
Featured
Like pumps, fans consume significant electrical energy while serving several applications. In many plants, the VFDs (variable ...
A frequency inverter controls AC motor speed. The frequency inverter converts the fixed supply frequency (60 Hz) to a ...
Motor starter (also known as soft starter, motor soft starter) is a electronic device integrates soft start, soft stop, ...
Soft starter allows the output voltage decreases gradually to achieve soft stop, in order to protect the equipment. Such as the ...
Soft Starter reduces electric motor starting current to 2-4 times during motor start up, reduces the impact to power grid during ...

In Discussion
Software modeling tools for the design of motors and generators
Can anybody know how to design a PCB using CNC machine?
Rewind an Existing motor rating 400 hp-3.3 kv, 4 pole
Equipments or instruments used for safety in distillation column?
Boiler Feed Water Pump
Modbus RS 485 - Daisy Chain Connection
How to know if the bearing of induction motor is healthy or not?
one cycle control
Can anybody know how to design a PCB using CNC machine?
Rewind an Existing motor rating 400 hp-3.3 kv, 4 pole
Equipments or instruments used for safety in distillation column?
Boiler Feed Water Pump
Modbus RS 485 - Daisy Chain Connection
How to know if the bearing of induction motor is healthy or not?
one cycle control