How to suppress chaotic operation in a DCM flyback at low load
I would like to share these tips with everybody.
A current mode controlled flyback converter always becomes unstable at low load due to the unavoidable leading edge current spike. It is not normally dangerous but as a design engineer I don’t like to look at it and listen to it.
Here are three useful and not patented tips.
First tip:
• Insert a low pass filter, say 1kohm + 100pF between current sense resistor and CS input in your control IC.
• Split the 1kohm in two resistors R1 to the fet and R2 to the control IC. R1 << R2.
• Insert 0,5 – 1pF between drain and the junction R1/R2. This can be made as a layer-to-layer capacitor in the PCB. It does not have to be a specific value.
• Adjust R1 until the spike in the junction in R1/R2 is cancelled.
You will see that the current spike is always proportional to the negative drain voltage step at turn-on. Once adjusted, the cancellation always follows the voltage step, and you some times achieve miracles with it. Cost = one resistor.
Second tip:
Having the low pass filter from first tip, add a small fraction of the gate driver output voltage to the current sense input, say 0,1V by inserting a large resistor from ‘Drive Out’ to ‘CS input’. The added low pass filtered step voltage will more or less conceal the current spike. You should reduce your current sense resistor accordingly. Cost = one resistor.
Third tip:
In a low power flyback, you some times just need an RC network or just an extra capacitor from drain to a DC point, either to reduce overshoot or to reduce noise. Connect the RC network or the capacitor to source, not to ground or Vcc. If you connect it to ground or Vcc, you will measure the added discharge current peak in the current sense resistor. Cost = nothing – just knowledge.
All tips can be used individually or combined => Less need for pre-load resistors on your output.
A current mode controlled flyback converter always becomes unstable at low load due to the unavoidable leading edge current spike. It is not normally dangerous but as a design engineer I don’t like to look at it and listen to it.
Here are three useful and not patented tips.
First tip:
• Insert a low pass filter, say 1kohm + 100pF between current sense resistor and CS input in your control IC.
• Split the 1kohm in two resistors R1 to the fet and R2 to the control IC. R1 << R2.
• Insert 0,5 – 1pF between drain and the junction R1/R2. This can be made as a layer-to-layer capacitor in the PCB. It does not have to be a specific value.
• Adjust R1 until the spike in the junction in R1/R2 is cancelled.
You will see that the current spike is always proportional to the negative drain voltage step at turn-on. Once adjusted, the cancellation always follows the voltage step, and you some times achieve miracles with it. Cost = one resistor.
Second tip:
Having the low pass filter from first tip, add a small fraction of the gate driver output voltage to the current sense input, say 0,1V by inserting a large resistor from ‘Drive Out’ to ‘CS input’. The added low pass filtered step voltage will more or less conceal the current spike. You should reduce your current sense resistor accordingly. Cost = one resistor.
Third tip:
In a low power flyback, you some times just need an RC network or just an extra capacitor from drain to a DC point, either to reduce overshoot or to reduce noise. Connect the RC network or the capacitor to source, not to ground or Vcc. If you connect it to ground or Vcc, you will measure the added discharge current peak in the current sense resistor. Cost = nothing – just knowledge.
All tips can be used individually or combined => Less need for pre-load resistors on your output.
You may also like:
What are the general guide lines for snubber circuit design in Inverter applications? When i referred the literature for snubber circuits for IGBT protection i found that we can either go for "individual" ...
Non-regenerative DC drives, also known as single-quadrant drives, rotate in one direction only & they have no inherent braking capabilities. Stopping the motor is done by removing voltage & allowing ...
Overcurrent protection uses as back-up protection for protection generators from faults between two windings of stator (two phases of stator). Setting of overcurrent protection depends from two settings: ...
I had small hills of dead MOSFETs and the directly attached controllers. When the first power MOSFETs emerged in 1979, I blew-up so many that I almost wrote them off. They had some real issues with D-S voltage ...
It will cause a series problems during AC drive operation in various environmental conditions, take an example as: when failure occurs, AC drives protective function is activated, and the AC drive tripped ...
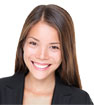
Featured
Like pumps, fans consume significant electrical energy while serving several applications. In many plants, the VFDs (variable ...
A frequency inverter controls AC motor speed. The frequency inverter converts the fixed supply frequency (60 Hz) to a ...
Motor starter (also known as soft starter, motor soft starter) is a electronic device integrates soft start, soft stop, ...
Soft starter allows the output voltage decreases gradually to achieve soft stop, in order to protect the equipment. Such as the ...
Soft Starter reduces electric motor starting current to 2-4 times during motor start up, reduces the impact to power grid during ...

In Discussion
Transformers in Parallel: The Myth
Voltage and frequency in finite bus
centum 3000 and new PCs problems
How good are analogue hall sensors as a form of position control?
Using Bridges for High Reliability Applications
Why it's 50 or 60 Hz, not 85 or 25hz
Is wondering why Ohio is slow in solar?
how the mirrors of solar panels move, to stay in the direction of the sun?
Voltage and frequency in finite bus
centum 3000 and new PCs problems
How good are analogue hall sensors as a form of position control?
Using Bridges for High Reliability Applications
Why it's 50 or 60 Hz, not 85 or 25hz
Is wondering why Ohio is slow in solar?
how the mirrors of solar panels move, to stay in the direction of the sun?