As far as I know all variable frequency drives with vector control can also be run with just V/F control.
A drive in vector control mode has several tuning parameters to increase or decrease motor performance. With factory default parameters a VFD in vector mode will have higher performance than a drive in V/F mode. Sort of like a "sport or racing" computer option in a modern automobile.
For long cables, the combination of cable impedance, high frequency input impedance of motor and VFD switching frequency can lead to reflection of voltage pulses that gives origin to large voltage overshoots on motor terminals. The problem increases as increasing switching frequency because the time between voltage pulses will be smaller, so, a voltage pulse reaching the motor will add to the pulse being reflected.
We recently evaluated a 500 HP 4 pole motor on a pump application. The motor is started with a soft starter. Upon examination of the bearings we discovered fluting inside both the variable frequency drive and opposite drive end bearings.
Our one frequency inverter which drives 0.37 KW 400 V dosing pump motor intermittently (once in a month or once in two months) shows DC link fault and the speed is reduced to zero.
Is it because of rewinding of the motor; winding geometry might have changed that affects the frequency inverter? If this is the problem then why this fault is not coming whenever it is in service? (It waits for 1month or two months some time the fault comes in a weak also)
Is it because of rewinding of the motor; winding geometry might have changed that affects the frequency inverter? If this is the problem then why this fault is not coming whenever it is in service? (It waits for 1month or two months some time the fault comes in a weak also)
The noise level created by the motor at any speed is in a fixed environment, take two motors same HP, Speed, Enclosure, and the applied voltage could be a factor of the noise, the installed conditions of a 1000 motors could vary from alignment to load, to piping connected to load, to actual load.
Babbitt Bearings, properly cared for and maintained will last much longer than anti-friction bearings. Properly set up and aligned there is no contact between the babbitt and the journal other that a scuff mark at the bottom that is caused by minimal contact at starting. As long as the motor is properly aligned to the load, the oil is kept clean and continually fed to the bearing the bearing will last a very long time.
Some motor manufacturers go from CU to Al because they try to reduce costs.
Then it just works the other way. Al wire needs to have a larger diameter than Cu if you want the same motor performance.
Then you may face problems with the slot opening and the slot fill, there may not even be enough space at all for the Al wire. You may need to change your lamination.
Then it just works the other way. Al wire needs to have a larger diameter than Cu if you want the same motor performance.
Then you may face problems with the slot opening and the slot fill, there may not even be enough space at all for the Al wire. You may need to change your lamination.
For a DC Motor Armature, There is a simple method of determining the condition of the Armature.
Drop Test Method: Give a DC Voltage across the commutator Segments for one pole pitch area from a Power supply or Battery. Connect Positive end of the DC power supply at one end and the Negative end at the opposite end.
I am currently investigating the design of a three phase axial flux PM motor, but replacing conventional materials with high temperature superconductors. I'm interested to know the thoughts of group members regarding design rules/rules of thumb relating to the number of stator coils and rotor poles. Many in the amateur wind turbine community seem to use a 4:3 ratio (magnets:coils), but I can't seem to find anything 'official' on the topic.
AC Motors - Variable torque: AC motors have a speed torque characteristic that varies as the square of the speed.
AC Motors - Constant torque: These ac motors can develop the same torque at each speed, thus power output varies directly with speed.
AC Motors - Constant torque: These ac motors can develop the same torque at each speed, thus power output varies directly with speed.
It's always best to first check with your VFD installation and operation documentation. It is likely that the drives manufacturer makes recommendations for reactor ratings. That said 3 to 5% reactance at the VFD drive's rated input current is always a good solution. If there is no internal bus choke or reactor in the VFD then use 5%. Don't sweat the voltage drop. The drop is in quadrature to the source voltage and so mostly subtracts at a 90 degree angle. Thus, the drop will be less than half the %reactance.
From a manufacturing economics standpoint, there is often a trade off in the decision to add a DC bus choke or not based on its ability to reduce the DC bus ripple. This is because it can reduce the DC bus capacitance necessary to present a clean DC source to the transistors. For some AC drive manufacturers who have the internal capability to wind their own component chokes, this often represents a component cost benefit compared to buying capacitors from outside vendors and being more subject to market volatility. On the other hand if the AC drive manufacturer IS also a manufacturer of capacitors, it works exactly the other way around.
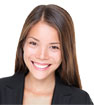
Featured
Like pumps, fans consume significant electrical energy while serving several applications. In many plants, the VFDs (variable ...
A frequency inverter controls AC motor speed. The frequency inverter converts the fixed supply frequency (60 Hz) to a ...
Motor starter (also known as soft starter, motor soft starter) is a electronic device integrates soft start, soft stop, ...
Soft starter allows the output voltage decreases gradually to achieve soft stop, in order to protect the equipment. Such as the ...
Soft Starter reduces electric motor starting current to 2-4 times during motor start up, reduces the impact to power grid during ...

In Discussion
Looking for a High Starting Torque Micro VFD
Use the sea as functional platform for the production of Solar Energy
8 Common SCADA Mistakes: EXPOSED
"Green Economy" Wind, Solar, Green Building, Geothermal are growing
3 stages Ejector Vacuum System
Feedre protection
Calculating 30min annual maximum demand on the substation transformer.
Pumping in salty conditions
Use the sea as functional platform for the production of Solar Energy
8 Common SCADA Mistakes: EXPOSED
"Green Economy" Wind, Solar, Green Building, Geothermal are growing
3 stages Ejector Vacuum System
Feedre protection
Calculating 30min annual maximum demand on the substation transformer.
Pumping in salty conditions