Home » Blog » Motor controls » Aluminum or copper wire in motors?
Aluminum or copper wire in motors?
Some motor manufacturers go from CU to Al because they try to reduce costs.
Then it just works the other way. Al wire needs to have a larger diameter than Cu if you want the same motor performance.
Then you may face problems with the slot opening and the slot fill, there may not even be enough space at all for the Al wire. You may need to change your lamination.
Furthermore, the blade gap of your inserting tools may not be suitable anymore so you will need a new set of toolings.
Also the end turns will have more volume which may cause problems at the end turn forming and even assembling process.
Besides, due to the properties of Al wire, your rejects will increase during the manufacturing process.
These are just a few examples.
Before changing to Al wire, manufacturers should consider the pros and cons carefully.
Some may invest more than they will safe with the cheaper Al wire.
Copper - at least at the purities and alloys used for electrical conductors - is fairly scarce, which tends to make the price pretty volatile. Aluminum, on the other hand, is fairly abundant in the alloys used for conductors ... and hence pretty stable in price (not to mention cheaper than copper).
Neither raw material (copper or aluminum) is used in its pure form for electrical conductors. Both have some other materials added, primarily for mechanical strength. The key factor in determining how much of each to use is the conductivity: 98 percent for the typical copper alloy (ref UNC C11000), 61 percent for the 1970s aluminum alloy (ref EC 1350), or 56 percent for the modern aluminum alloys used in busbar material (ref alloy 6101).
Material properties:
Tensile strength (same cross section) lb/in2: Cu = 50000 Al = 32000
Tensile strength (same conductivity) lb/in2: Cu = 50000 Al = 50000
Weight (same conductivity) lb : Cu = 100 Al = 54
Cross section (same conductivity) % : Cu = 100 Al = 156
Coefficient expansion per deg C x 10^-6 : Cu = 16.6 Al = 23.0
The choice between Al and Cu usually boils down to either cost or weight.
Care must be taken because Al is not as strong (more problems with the forces generated by fault conditions) AND because it has a higher susceptibility to dimensional change under high temperature conditions (such as those occurring during electrical faults).
Another consideration for an aluminum-winding machine are the connection points for real-world transmission: care in terminations is a must. Galvanic action between dissimiar materials is a known difficulty that can be further aggravated by airborne (chemical) contaminants.
Then it just works the other way. Al wire needs to have a larger diameter than Cu if you want the same motor performance.
Then you may face problems with the slot opening and the slot fill, there may not even be enough space at all for the Al wire. You may need to change your lamination.
Furthermore, the blade gap of your inserting tools may not be suitable anymore so you will need a new set of toolings.
Also the end turns will have more volume which may cause problems at the end turn forming and even assembling process.
Besides, due to the properties of Al wire, your rejects will increase during the manufacturing process.
These are just a few examples.
Before changing to Al wire, manufacturers should consider the pros and cons carefully.
Some may invest more than they will safe with the cheaper Al wire.
Copper - at least at the purities and alloys used for electrical conductors - is fairly scarce, which tends to make the price pretty volatile. Aluminum, on the other hand, is fairly abundant in the alloys used for conductors ... and hence pretty stable in price (not to mention cheaper than copper).
Neither raw material (copper or aluminum) is used in its pure form for electrical conductors. Both have some other materials added, primarily for mechanical strength. The key factor in determining how much of each to use is the conductivity: 98 percent for the typical copper alloy (ref UNC C11000), 61 percent for the 1970s aluminum alloy (ref EC 1350), or 56 percent for the modern aluminum alloys used in busbar material (ref alloy 6101).
Material properties:
Tensile strength (same cross section) lb/in2: Cu = 50000 Al = 32000
Tensile strength (same conductivity) lb/in2: Cu = 50000 Al = 50000
Weight (same conductivity) lb : Cu = 100 Al = 54
Cross section (same conductivity) % : Cu = 100 Al = 156
Coefficient expansion per deg C x 10^-6 : Cu = 16.6 Al = 23.0
The choice between Al and Cu usually boils down to either cost or weight.
Care must be taken because Al is not as strong (more problems with the forces generated by fault conditions) AND because it has a higher susceptibility to dimensional change under high temperature conditions (such as those occurring during electrical faults).
Another consideration for an aluminum-winding machine are the connection points for real-world transmission: care in terminations is a must. Galvanic action between dissimiar materials is a known difficulty that can be further aggravated by airborne (chemical) contaminants.
You may also like:
We recently evaluated a 500 HP 4 pole motor on a pump application. The motor is started with a soft starter. Upon examination of the bearings we discovered fluting inside both the variable frequency drive and ...
If S ≤ 16 then the Minimum cross-sectional area of the corresponding earth conductor = S mm2
If 16 < S ≤ 35 then the Minimum cross-sectional area of the corresponding earth conductor = 16 mm2
if S > 16 ...
The concept of home automation on a global scale is a good concept. How to implement such a technology on a global scale is an interesting problem, or I should say issues to be resolved. Before global approval ...
There being a lot more than 12 guidelines to follow. In my experience, there are plenty of people that can design a panel but if they haven't gone to the field with it then they haven't been able to learn from ...
Usually in your case there should be Electrical as well as Mechanical interlocks between the mains incomer & genset main breaker. ie both Sources will never be in Synchronism ( will not feeding the same ...
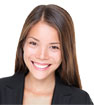
Featured
Like pumps, fans consume significant electrical energy while serving several applications. In many plants, the VFDs (variable ...
A frequency inverter controls AC motor speed. The frequency inverter converts the fixed supply frequency (60 Hz) to a ...
Motor starter (also known as soft starter, motor soft starter) is a electronic device integrates soft start, soft stop, ...
Soft starter allows the output voltage decreases gradually to achieve soft stop, in order to protect the equipment. Such as the ...
Soft Starter reduces electric motor starting current to 2-4 times during motor start up, reduces the impact to power grid during ...

In Discussion
5MW SPV projects India
Current distribution in sub-transmission network
Why would you design your own power supply?
Open delta voltage?
How to implement winder application with tension control?
What is the most severe transient symmetrical fault
voltage drop during motor starting
Control panel cable wiring
Current distribution in sub-transmission network
Why would you design your own power supply?
Open delta voltage?
How to implement winder application with tension control?
What is the most severe transient symmetrical fault
voltage drop during motor starting
Control panel cable wiring