Home » Blog » Experience » Induction machines testing
Induction machines testing
Case: We got by testing 3 different machines under no-load condition.
The 50 HP and 3 HP are the ones which behave abnormally when we apply 10% overvoltage. The third machine (7.5 HP) is a machine that reacts normally under the same condition.
What we mean by abnormal behavior is the input power of the machine that will increase dramatically under only 10% overvoltage which is not the case with most of the induction machines. This can be seen by the numbers given below.
50 HP, 575V
Under 10% overvoltage:
Friction & Windage Losses increase 0.2%
Core loss increases 102%
Stator Copper Loss increases 107%
3 HP, 208V
Under 10% overvoltage:
Friction & Windage Losses increase 8%
Core loss increases 34%
Stator Copper Loss increases 63%
7.5 HP, 460V
Under 10% overvoltage:
Friction & Windage Losses decrease 1%
Core loss increases 22%
Stator Copper Loss increases 31%
Till now, we couldn't diagnose the exact reason that pushes those two machines to behave in such way.
Answer: A few other things I have not seen (yet) include the following:
1) Are the measurements of voltage and current being made by "true RMS" devices or not?
2) Actual measurements for both current and voltage should be taken simultaneously (with a "true RMS" device) for all phases.
3) Measurements of voltage and current should be taken at the motor terminals, not at the drive output.
4) Measurement of output waveform frequency (for each phase), and actual rotational speed of the motor shaft.
These should all be done at each point on the curve.
The reason for looking at the phase relationships of voltage and current is to ensure the incoming power is balanced. Even a small voltage imbalance (say, 3 percent) may result in a significant current imbalance (often 10 percent or more). This unbalanced supply will lead to increased (or at least unexpected) losses, even at relatively light loads. Also - the unbalance is more obvious at lightly loaded conditions.
As noted above, friction and windage losses are speed dependent: the "approximate" relationship is against square of speed.
Things to note about how the machine should perform under normal circumstances:
1. The flux densities in the magnetic circuit are going to increase proportionally with the voltage. This means +10% volts means +10% flux. However, the magnetizing current requirement varies more like the square of the voltage (+10% volt >> +18-20% mag amps).
2. Stator core loss is proportional to the square of the voltage (+10% V >> +20-25% kW).
3. Stator copper loss is proportional to the square of the current (+10% V >> +40-50% kW).
4. Rotor copper loss is independent of voltage change (+10% V >> +0 kW).
5. Assuming speed remains constant, friction and windage are unaffected (+10% V >> +0 kW). Note that with a change of 10% volts, it is highly likely that the speed WILL actually change!
6. Stator eddy loss is proportional to square of voltage (+10% V >> +20-25% kW). Note that stator eddy loss is often included as part of the "stray" calculation under IEEE 112. The other portions of the "stray" value are relatively independent of voltage.
Looking at your test results it would appear that the 50 HP machine is:
a) very highly saturated
b) has damaged/shorted laminations
c) has a different grade of electrical steel (compared to the other ratings)
d) has damaged stator windings (possibly from operation on the drive, particularly if it has a very high dv/dt and/or high common-mode voltage characteristic)
e) a combination of any/all of the above.
One last question - are all the machines rated for the same operating speed (measured in RPM)? It is probable that "special duty" machines are designed differently in terms of saturation and response when compared to "standard" designs.
The 50 HP and 3 HP are the ones which behave abnormally when we apply 10% overvoltage. The third machine (7.5 HP) is a machine that reacts normally under the same condition.
What we mean by abnormal behavior is the input power of the machine that will increase dramatically under only 10% overvoltage which is not the case with most of the induction machines. This can be seen by the numbers given below.
50 HP, 575V
Under 10% overvoltage:
Friction & Windage Losses increase 0.2%
Core loss increases 102%
Stator Copper Loss increases 107%
3 HP, 208V
Under 10% overvoltage:
Friction & Windage Losses increase 8%
Core loss increases 34%
Stator Copper Loss increases 63%
7.5 HP, 460V
Under 10% overvoltage:
Friction & Windage Losses decrease 1%
Core loss increases 22%
Stator Copper Loss increases 31%
Till now, we couldn't diagnose the exact reason that pushes those two machines to behave in such way.
Answer: A few other things I have not seen (yet) include the following:
1) Are the measurements of voltage and current being made by "true RMS" devices or not?
2) Actual measurements for both current and voltage should be taken simultaneously (with a "true RMS" device) for all phases.
3) Measurements of voltage and current should be taken at the motor terminals, not at the drive output.
4) Measurement of output waveform frequency (for each phase), and actual rotational speed of the motor shaft.
These should all be done at each point on the curve.
The reason for looking at the phase relationships of voltage and current is to ensure the incoming power is balanced. Even a small voltage imbalance (say, 3 percent) may result in a significant current imbalance (often 10 percent or more). This unbalanced supply will lead to increased (or at least unexpected) losses, even at relatively light loads. Also - the unbalance is more obvious at lightly loaded conditions.
As noted above, friction and windage losses are speed dependent: the "approximate" relationship is against square of speed.
Things to note about how the machine should perform under normal circumstances:
1. The flux densities in the magnetic circuit are going to increase proportionally with the voltage. This means +10% volts means +10% flux. However, the magnetizing current requirement varies more like the square of the voltage (+10% volt >> +18-20% mag amps).
2. Stator core loss is proportional to the square of the voltage (+10% V >> +20-25% kW).
3. Stator copper loss is proportional to the square of the current (+10% V >> +40-50% kW).
4. Rotor copper loss is independent of voltage change (+10% V >> +0 kW).
5. Assuming speed remains constant, friction and windage are unaffected (+10% V >> +0 kW). Note that with a change of 10% volts, it is highly likely that the speed WILL actually change!
6. Stator eddy loss is proportional to square of voltage (+10% V >> +20-25% kW). Note that stator eddy loss is often included as part of the "stray" calculation under IEEE 112. The other portions of the "stray" value are relatively independent of voltage.
Looking at your test results it would appear that the 50 HP machine is:
a) very highly saturated
b) has damaged/shorted laminations
c) has a different grade of electrical steel (compared to the other ratings)
d) has damaged stator windings (possibly from operation on the drive, particularly if it has a very high dv/dt and/or high common-mode voltage characteristic)
e) a combination of any/all of the above.
One last question - are all the machines rated for the same operating speed (measured in RPM)? It is probable that "special duty" machines are designed differently in terms of saturation and response when compared to "standard" designs.
You may also like:
There are several issues at work here. For high AC current inductors, you want to have low core losses, low proximity loss in the windings, and low fringing effects.
At normal frequencies, ferrites are by far ...
Is there a way of connecting a three phase pressure control switch on a three phase motor. Also is there a three phase float switch for a three phase submersible pump i know of a single phase switch.
The ...
Controlled bridge rectifiers are not limited to single-phase designs. In most commercial & industrial control systems, AC power is available in three-phase form for maxi mum horsepower & efficiency. ...
Make sure your generator can start your largest motor and that your disconnect breaker or fuses can handle the inrush. I have seen this as an issue, especially when soft starters are used. Soft starters lower ...
When I was doing my PhD in motor design of reluctance machines with flux assistance (switched reluctance machines and flux switching machines with magnets and/or permanently energised coils) my supervisor was ...
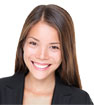
Featured
Like pumps, fans consume significant electrical energy while serving several applications. In many plants, the VFDs (variable ...
A frequency inverter controls AC motor speed. The frequency inverter converts the fixed supply frequency (60 Hz) to a ...
Motor starter (also known as soft starter, motor soft starter) is a electronic device integrates soft start, soft stop, ...
Soft starter allows the output voltage decreases gradually to achieve soft stop, in order to protect the equipment. Such as the ...
Soft Starter reduces electric motor starting current to 2-4 times during motor start up, reduces the impact to power grid during ...

In Discussion
VFD Quadrant Operation
Delta VFD with PLC controls
Sequence impedances
Current Transformer applications interchange
Which solar panels are best suited for a large solar farm?
Line to line is big faults (short) that occurs from power supply
Who can help in sales of solar photovoltaic grid-tied inverters?
Different vendors for HMI and Automation Engineering Software
Delta VFD with PLC controls
Sequence impedances
Current Transformer applications interchange
Which solar panels are best suited for a large solar farm?
Line to line is big faults (short) that occurs from power supply
Who can help in sales of solar photovoltaic grid-tied inverters?
Different vendors for HMI and Automation Engineering Software