Three Phase Input DC Drive
Controlled bridge rectifiers are not limited to single-phase designs. In most commercial & industrial control systems, AC power is available in three-phase form for maxi mum horsepower & efficiency. Typically six SCRs are connected together, to make a three-phase fully controlled rectifier. This three-phase bridge rectifier circuit has three legs, each phase connected to one of the three phase voltages. It can be seen that the bridge circuit has two halves, the positive half consisting of the SCRs S1, S3, & S5 & the negative half consisting of the SCRs S2, S4, & S6. At any time when there is current flow, one SCR from each half conducts.
The variable DC output voltage from the rectifier sup plies voltage to the motor armature in order to run it at the desired speed. The gate firing angle of the SCRs in the bridge rectifier, along with the maximum positive & negative values of the AC sine wave, determine the value of the motor armature voltage. The motor draws current from the three-phase AC power source in proportion to the amount of mechanical load applied to the motor shaft. Unlike AC drives, bypassing the drive to run the motor is not possible.
Larger-horsepower three-phase drive panels often consist of a power module mounted on a chassis with line fuses & disconnect. This design simplifies mounting & makes connecting power cables easier as well. A three phase input DC drive with the following drive power specifications:
The variable DC output voltage from the rectifier sup plies voltage to the motor armature in order to run it at the desired speed. The gate firing angle of the SCRs in the bridge rectifier, along with the maximum positive & negative values of the AC sine wave, determine the value of the motor armature voltage. The motor draws current from the three-phase AC power source in proportion to the amount of mechanical load applied to the motor shaft. Unlike AC drives, bypassing the drive to run the motor is not possible.
Larger-horsepower three-phase drive panels often consist of a power module mounted on a chassis with line fuses & disconnect. This design simplifies mounting & makes connecting power cables easier as well. A three phase input DC drive with the following drive power specifications:
- Nominal line voltage for three-phase-230/460 V AC
- Voltage variation-+15%, -10% of nominal
- Nominal line frequency-50 or 60 cycles per second
- DC voltage rating 230 V AC line: Armature voltage 240 V DC; field voltage 150 V DC
- DC voltage rating 460 V AC line: Armature voltage 500 V DC; field voltage 300 V DC
You may also like:
Is there a way of connecting a three phase pressure control switch on a three phase motor. Also is there a three phase float switch for a three phase submersible pump i know of a single phase switch.
The ...
Make sure your generator can start your largest motor and that your disconnect breaker or fuses can handle the inrush. I have seen this as an issue, especially when soft starters are used. Soft starters lower ...
We got by testing 3 different machines under no-load condition.
The 50 HP and 3 HP are the ones which behave abnormally when we apply 10% overvoltage. The third machine (7.5 HP) is a machine that reacts ...
There are several issues at work here. For high AC current inductors, you want to have low core losses, low proximity loss in the windings, and low fringing effects.
At normal frequencies, ferrites are by far ...
When I was doing my PhD in motor design of reluctance machines with flux assistance (switched reluctance machines and flux switching machines with magnets and/or permanently energised coils) my supervisor was ...
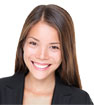
Featured
Like pumps, fans consume significant electrical energy while serving several applications. In many plants, the VFDs (variable ...
A frequency inverter controls AC motor speed. The frequency inverter converts the fixed supply frequency (60 Hz) to a ...
Motor starter (also known as soft starter, motor soft starter) is a electronic device integrates soft start, soft stop, ...
Soft starter allows the output voltage decreases gradually to achieve soft stop, in order to protect the equipment. Such as the ...
Soft Starter reduces electric motor starting current to 2-4 times during motor start up, reduces the impact to power grid during ...

In Discussion
Solar Module Lamination Cycle Time Optimization
Different vendors for HMI and Automation Engineering Software
Powder suspension in the liquid
How to decide switching frequency of SMPS?
Who can help in sales of solar photovoltaic grid-tied inverters?
Line to line is big faults (short) that occurs from power supply
PV Module prices from Indian manufacturers
Keep the Documentation Clear and Simple
Different vendors for HMI and Automation Engineering Software
Powder suspension in the liquid
How to decide switching frequency of SMPS?
Who can help in sales of solar photovoltaic grid-tied inverters?
Line to line is big faults (short) that occurs from power supply
PV Module prices from Indian manufacturers
Keep the Documentation Clear and Simple