Home » Blog » Experience » Cleaning solvent for motor windings
Cleaning solvent for motor windings
Usually, the dry ice approach is the best bet because it leaves no real residue from the cleaning material. If the insulation is "fluffing", the likely problem is that the air pressure used to move the dry ice particles is too high.
A second alternative that can be used is "corn cob blasting". The media is reusable, biodegradable particles of corn husks. Again, a relatively low pressure air stream is required. It WILL damage the insulation if the pressure is too high, just as in the dry ice case.
Most solvents will aggressively attack the insulation systems used for windings: this is specifically true for the larger machines where mica tapes are coated / filled with a resinous material (vacuum pressure impregnation). However, it is equally true for smaller machines where the primary insulation is at the strand level and is essentially a varnish or enamel coating on the wire. If you're worried about how the solvent will affect the insulation system, get in touch with the motor supplier for their suggested approach.
If a solvent-based cleaner must be used, it should be applied sparingly - BY HAND - on the areas to be cleaned to break up the oily / greasy contaminant and then rewashed with some other (non-solvent) approach to clean away any solvent residue. This also will require a "dry out" of the equipment after the second washing. This three-stage approach tends to minimize damage done by solvent that may be left behind to "eat away" at the varnishes, enamels, and resins comprising the insulation system.
One last thing - pretty much ALL solvents are going to be designated as hazardous materials in most regions, due to health concerns. Therefore it is more a case of "pick your poison"!
A second alternative that can be used is "corn cob blasting". The media is reusable, biodegradable particles of corn husks. Again, a relatively low pressure air stream is required. It WILL damage the insulation if the pressure is too high, just as in the dry ice case.
Most solvents will aggressively attack the insulation systems used for windings: this is specifically true for the larger machines where mica tapes are coated / filled with a resinous material (vacuum pressure impregnation). However, it is equally true for smaller machines where the primary insulation is at the strand level and is essentially a varnish or enamel coating on the wire. If you're worried about how the solvent will affect the insulation system, get in touch with the motor supplier for their suggested approach.
If a solvent-based cleaner must be used, it should be applied sparingly - BY HAND - on the areas to be cleaned to break up the oily / greasy contaminant and then rewashed with some other (non-solvent) approach to clean away any solvent residue. This also will require a "dry out" of the equipment after the second washing. This three-stage approach tends to minimize damage done by solvent that may be left behind to "eat away" at the varnishes, enamels, and resins comprising the insulation system.
One last thing - pretty much ALL solvents are going to be designated as hazardous materials in most regions, due to health concerns. Therefore it is more a case of "pick your poison"!
You may also like:
Present renewable energy policy is allowing these profit making companies to avoid paying taxes, and own the assets due to such FREE EQUITY, which belongs to the Government, thus Accelerated Depreciation (AD) ...
In inverter regular inspection, we must cut off power before operation. Wait 4minutes (the bigger the longer, the maximum waiting time is 15 minutes) till the frequency inverter display panel LED indicator ...
The aforementioned types of Circuit Breakers are used in LV System and generally based on the same operating principle.
MCB and MCCB/ICCB have a bimetal heater for overload which releases the Contact s while ...
When operating an AC machine on a variable frequency drive, the most common approach is to mimic the DC curves. This is done by using a constant volt/hertz ratio until a "base" speed is achieved at rated ...
For flyback & boost applications, powder cores such as Kool-mu, Xmu, etc... are usually best performing and lowest cost. Even these may need to be gapped and if CCM operation is required, a "stepped-gap" ...
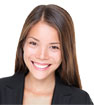
Featured
Like pumps, fans consume significant electrical energy while serving several applications. In many plants, the VFDs (variable ...
A frequency inverter controls AC motor speed. The frequency inverter converts the fixed supply frequency (60 Hz) to a ...
Motor starter (also known as soft starter, motor soft starter) is a electronic device integrates soft start, soft stop, ...
Soft starter allows the output voltage decreases gradually to achieve soft stop, in order to protect the equipment. Such as the ...
Soft Starter reduces electric motor starting current to 2-4 times during motor start up, reduces the impact to power grid during ...

In Discussion
ABB LCD for pH display shown fault in field but functioning during lab test
Automated palletizing - Looking for your input
How to find solar sunhour/day using solar irradiation values?
Overload of Generator and its response?
RS 485 replacing RS 232 or not
Starting solar electricity price for a good quality
Dataloging with Micrologix 1400
Gapping flyback cores / Distributed gap cores
Automated palletizing - Looking for your input
How to find solar sunhour/day using solar irradiation values?
Overload of Generator and its response?
RS 485 replacing RS 232 or not
Starting solar electricity price for a good quality
Dataloging with Micrologix 1400
Gapping flyback cores / Distributed gap cores