Home » Blog » Energy saving » Transformer Saturation
Transformer Saturation
Transformer saturates because of increase primary voltage. Increase primary voltage has a consequence increase of intensity of magnetic field and magnetic induction until "knee point voltage" at the magnetising curve. From "knee point voltage", if voltage increases, then intensity of magnetic field also increases, but magnetic induction stays almost equal like as before increasing of voltage or it increases a little (a lot less than in linear area)... This area of magnetising curve is called area of saturation. Area of saturation is very dangerous area for work of transformer, because in this area ferromagnetic core is warming more than in linear area, so it has a consequence damaging of ferromagnetic core.
The transformer core can saturate due to, High Voltage, Low Frequency or a combination of both. Protection element V/Hz (ANSI 24) can be used to protect the transformer against over excitation as this can cause damage due to overheating / excessive core loss. This protection element is commonly used on generator step-up transformers.
Another reason that I can now think of is if you have a DC component in you excitation voltage. This can happen if your neutral point is at an elevated voltage. This can happen due to various reasons. One is geomagnetic induced currents caused by the interaction between the sun's flares and our earths magnetic field. Other reasons may be purely a bad quality neutral point which is subjected to sources of induced currents. Railway transformers sometimes have problems with this since they are installed near railways -which if not properly grounded -may cause an elevated neutral voltage.
In case of Generator transformers, an overfluxing protection is provided to safeguard the transformer against over excitation by generators and during load throw off condition. Generator transformers are also specified to have the capability to withstand the over fluxing condition viz 110%- continuous; 125%- for 60 seconds; 140%-for 5 seconds.
The transformer core can saturate due to, High Voltage, Low Frequency or a combination of both. Protection element V/Hz (ANSI 24) can be used to protect the transformer against over excitation as this can cause damage due to overheating / excessive core loss. This protection element is commonly used on generator step-up transformers.
Another reason that I can now think of is if you have a DC component in you excitation voltage. This can happen if your neutral point is at an elevated voltage. This can happen due to various reasons. One is geomagnetic induced currents caused by the interaction between the sun's flares and our earths magnetic field. Other reasons may be purely a bad quality neutral point which is subjected to sources of induced currents. Railway transformers sometimes have problems with this since they are installed near railways -which if not properly grounded -may cause an elevated neutral voltage.
In case of Generator transformers, an overfluxing protection is provided to safeguard the transformer against over excitation by generators and during load throw off condition. Generator transformers are also specified to have the capability to withstand the over fluxing condition viz 110%- continuous; 125%- for 60 seconds; 140%-for 5 seconds.
Tag: Transformer
You may also like:
I have a problem with ABB ACS800-104-0105-3 drive model, the output current reading on the VFD is always double the reading of the clamp ampere(i.e. drive reading= 40 A, clamp ampere reading=20 A), what is the ...
In speaking with many engineers over several decades, a large manufacture of large electric motors, have decided once a rotor is identified as the problem, rebarring, or any single repair is usually ...
The second category, the motor design software, is specifically designed for motor analysis. It can be magnetic circuit based such as SPEED and RMXprt or full finite element based such as MotorSolve. The ...
Quality frequency inverters incorporate either an AC Reactor or DC Reactor (choke). Their inclusion in the basic design of the frequency inverter allows the design engineer to maximize the advantages of the ...
1: Torque boost: this function is the variable speed drive increases output voltage (mainly in low frequency) to compensate the torque loss due to voltage drop in the stator resistance, thereby improving the ...
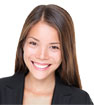
Featured
Like pumps, fans consume significant electrical energy while serving several applications. In many plants, the VFDs (variable ...
A frequency inverter controls AC motor speed. The frequency inverter converts the fixed supply frequency (60 Hz) to a ...
Motor starter (also known as soft starter, motor soft starter) is a electronic device integrates soft start, soft stop, ...
Soft starter allows the output voltage decreases gradually to achieve soft stop, in order to protect the equipment. Such as the ...
Soft Starter reduces electric motor starting current to 2-4 times during motor start up, reduces the impact to power grid during ...

In Discussion
Recommendations for Motion Control Industry Marketing and Sales
Rewind an Existing motor rating 400 hp-3.3 kv, 4 pole
PID control in DCS systems
Cu320-2 PN
queries regarding setting up solar power plant
Shading Effect
why Generator transformer HV winding is STAR connected.
Can the rotor resistance drop down from its design value?
Rewind an Existing motor rating 400 hp-3.3 kv, 4 pole
PID control in DCS systems
Cu320-2 PN
queries regarding setting up solar power plant
Shading Effect
why Generator transformer HV winding is STAR connected.
Can the rotor resistance drop down from its design value?