Home » Blog » Motor controls » Motor testing and repairing
Motor testing and repairing
Are you having noticeable performance problems with these motors? The size and type of motor are critical as mentioned, a cast rotor with the right testing can pick up voids in the bar and resistance rings, not necessarily a problem as most mass produced cast bar rotors will have some sort of voids in the bars, and the motors are fine, the red flag comes up when using these black box tests, which picks up what appears to be a problem but is actually just a normal condition from the manufacturing process.
I have very little faith that any one test on an assembled motor, can tell the user everything about the condition of the internals, or health of the motor.
When you consider all the testing the health field can use, such as a full body scan, many times it leads to false alarms and more expensive testing.
I could ask a few dozen questions on the age, type, past testing, past history of the motors in question, but if you are basing the health or life expectancy of any motor by only the use of testing without a visual of the internals of a motor, those questions need to be addressed to the supplier of the testing equipment.
I believe in predictive maintenance, by vibration charting, insulation value testing, surge testing, all charted and plotted over time.
When you have insulation values at 100 megohms in March, and then 500 in July, it is likely the ambient conditions have effect on the readings. Dependent on the ambient conditions and area the motors are located, humidity in March is gone in July. So plotting the readings over time will give a plot to see if the trend is downward regardless, or it could be the readings in March are fairly constant, the readings in July are constant, but there is no downward plot of the insulation value.
When you get insulation values in March of 100 megohms, and again in July but the megger readings are now 60, then a user would want to decrease the time between testings, starting with say quarterly, once you develop a plot, if that plot changes downward, then it is time to test maybe even weekly as it may show some kind of insulation breakdown, or contaminates that would call for a visual inspection and possible cleaning/repair of the motor.
Same with plotting surge tests.
Same with plotting vibration testing.
But the answers to these questions where the test results are confusing at best, need to be addressed to the testing equipment provider.
I have yet to see any demonstration of a total motor health testing device, that did not have some caveat dependent on the speed or other design factors of particular motors.
Maybe these tests were not confusing prior to now, if so, I doubt two identical motors would fail/start to fail with the same exact type of problem.
Again I could ask a dozen questions such as are the motors new, is this the first time you have results that make no sense, and as much of the total history of the motors and testing programs you have in place.
When it comes to rotors, testing is critical, and often when problems are found with the motor, and all testing points to the rotor, often simply repairing the rotor will not resolve the problem.
In speaking with many engineers over several decades, a large manufacture of large electric motors, have decided once a rotor is identified as the problem, rebarring, or any single repair is usually unsuccessful, and their procedure is to scrap the rotor completely.
I have very little faith that any one test on an assembled motor, can tell the user everything about the condition of the internals, or health of the motor.
When you consider all the testing the health field can use, such as a full body scan, many times it leads to false alarms and more expensive testing.
I could ask a few dozen questions on the age, type, past testing, past history of the motors in question, but if you are basing the health or life expectancy of any motor by only the use of testing without a visual of the internals of a motor, those questions need to be addressed to the supplier of the testing equipment.
I believe in predictive maintenance, by vibration charting, insulation value testing, surge testing, all charted and plotted over time.
When you have insulation values at 100 megohms in March, and then 500 in July, it is likely the ambient conditions have effect on the readings. Dependent on the ambient conditions and area the motors are located, humidity in March is gone in July. So plotting the readings over time will give a plot to see if the trend is downward regardless, or it could be the readings in March are fairly constant, the readings in July are constant, but there is no downward plot of the insulation value.
When you get insulation values in March of 100 megohms, and again in July but the megger readings are now 60, then a user would want to decrease the time between testings, starting with say quarterly, once you develop a plot, if that plot changes downward, then it is time to test maybe even weekly as it may show some kind of insulation breakdown, or contaminates that would call for a visual inspection and possible cleaning/repair of the motor.
Same with plotting surge tests.
Same with plotting vibration testing.
But the answers to these questions where the test results are confusing at best, need to be addressed to the testing equipment provider.
I have yet to see any demonstration of a total motor health testing device, that did not have some caveat dependent on the speed or other design factors of particular motors.
Maybe these tests were not confusing prior to now, if so, I doubt two identical motors would fail/start to fail with the same exact type of problem.
Again I could ask a dozen questions such as are the motors new, is this the first time you have results that make no sense, and as much of the total history of the motors and testing programs you have in place.
When it comes to rotors, testing is critical, and often when problems are found with the motor, and all testing points to the rotor, often simply repairing the rotor will not resolve the problem.
In speaking with many engineers over several decades, a large manufacture of large electric motors, have decided once a rotor is identified as the problem, rebarring, or any single repair is usually unsuccessful, and their procedure is to scrap the rotor completely.
You may also like:
I have a problem with ABB ACS800-104-0105-3 drive model, the output current reading on the VFD is always double the reading of the clamp ampere(i.e. drive reading= 40 A, clamp ampere reading=20 A), what is the ...
The transformer core can saturate due to, High Voltage, Low Frequency or a combination of both. Protection element V/Hz (ANSI 24) can be used to protect the transformer against over excitation as this can ...
1: Torque boost: this function is the variable speed drive increases output voltage (mainly in low frequency) to compensate the torque loss due to voltage drop in the stator resistance, thereby improving the ...
The second category, the motor design software, is specifically designed for motor analysis. It can be magnetic circuit based such as SPEED and RMXprt or full finite element based such as MotorSolve. The ...
Quality frequency inverters incorporate either an AC Reactor or DC Reactor (choke). Their inclusion in the basic design of the frequency inverter allows the design engineer to maximize the advantages of the ...
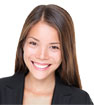
Featured
Like pumps, fans consume significant electrical energy while serving several applications. In many plants, the VFDs (variable ...
A frequency inverter controls AC motor speed. The frequency inverter converts the fixed supply frequency (60 Hz) to a ...
Motor starter (also known as soft starter, motor soft starter) is a electronic device integrates soft start, soft stop, ...
Soft starter allows the output voltage decreases gradually to achieve soft stop, in order to protect the equipment. Such as the ...
Soft Starter reduces electric motor starting current to 2-4 times during motor start up, reduces the impact to power grid during ...

In Discussion
Can the rotor resistance drop down from its design value?
One cycle control for PFC or general DC/DC?
Cu320-2 PN
PID control in DCS systems
flyback converter design
Recommendations for Motion Control Industry Marketing and Sales
Rewind an Existing motor rating 400 hp-3.3 kv, 4 pole
Does anyone know what is life cycle for solar panel?
One cycle control for PFC or general DC/DC?
Cu320-2 PN
PID control in DCS systems
flyback converter design
Recommendations for Motion Control Industry Marketing and Sales
Rewind an Existing motor rating 400 hp-3.3 kv, 4 pole
Does anyone know what is life cycle for solar panel?