Synchronous motors VS induction motors
1- Synchronous motors generally offer more efficiency than induction ones, and hence in higher ratings (about 5000 hp and higher) they may be more cost effective considering Life Cycle Costs. The exact size of preference to switch to Synchronous shall be determined based on LCC analysis of specific application.
2- A Large reciprocating compressor is a highly variable load and a synchronous motor will keep its speed in this situation while the induction motor would respond with fluctuating speed.
3- Based on API 618 (with reference to IEC and NEMA), a synchronous motor used for reciprocating compressor may tolerate 66% variation in current, while an induction motor is allowed to have only 40% variation in current which in larger compressors may be exceeded (because of variable load).Also Higher efficiency induction motors with less slip, cause more current variations and are prohibited.
Synchronous motors are characterized by limited starting torque, the ability to actively control power factor and less current in-rush than the induction motor. The synchronous motor also requires active matching of torque demand with motor output. Synchronous motors started “across-the–line” also produce oscillatory torques at the twice slip frequency during acceleration (i.e., starting at 120 Hz and decreasing to 0 Hz at full speed). These torques generally require additional transient torsional analysis because of the potential for damage.
Synchronous motors are usually advantageous on slow speed applications (e.g., low speed reciprocating compressors operating from 200-400 RPM) and also on machines larger than about 10,000 to 15,000 HP. With both motor types, it is important to match the compressor torque versus speed requirements with motor torque versus speed capabilities as discussed in Sections 6.0 and 7.0. Both induction and synchronous motor types can be coupled with a VFD for variable speed operation.
If the motor is being driven by a variable frequency drive with sophisticated drive algorithms, i.e. controllers that can track the load torque variations, then both the efficiency and transient stability problems can be solved together.
The other significant thing is the starting problem. The transient load torque is also present at starting so the motor has to be able to accelerate through the load transients and be capable of starting when the compressor is sitting at the highest load.
2- A Large reciprocating compressor is a highly variable load and a synchronous motor will keep its speed in this situation while the induction motor would respond with fluctuating speed.
3- Based on API 618 (with reference to IEC and NEMA), a synchronous motor used for reciprocating compressor may tolerate 66% variation in current, while an induction motor is allowed to have only 40% variation in current which in larger compressors may be exceeded (because of variable load).Also Higher efficiency induction motors with less slip, cause more current variations and are prohibited.
Synchronous motors are characterized by limited starting torque, the ability to actively control power factor and less current in-rush than the induction motor. The synchronous motor also requires active matching of torque demand with motor output. Synchronous motors started “across-the–line” also produce oscillatory torques at the twice slip frequency during acceleration (i.e., starting at 120 Hz and decreasing to 0 Hz at full speed). These torques generally require additional transient torsional analysis because of the potential for damage.
Synchronous motors are usually advantageous on slow speed applications (e.g., low speed reciprocating compressors operating from 200-400 RPM) and also on machines larger than about 10,000 to 15,000 HP. With both motor types, it is important to match the compressor torque versus speed requirements with motor torque versus speed capabilities as discussed in Sections 6.0 and 7.0. Both induction and synchronous motor types can be coupled with a VFD for variable speed operation.
If the motor is being driven by a variable frequency drive with sophisticated drive algorithms, i.e. controllers that can track the load torque variations, then both the efficiency and transient stability problems can be solved together.
The other significant thing is the starting problem. The transient load torque is also present at starting so the motor has to be able to accelerate through the load transients and be capable of starting when the compressor is sitting at the highest load.
You may also like:
Many years ago we used to call this the "what ifs?". Part of the design phase is when we model what we think the system is meant to do. Just as important is how the system is meant to react when things are not ...
DC drives with motor field control provide coordinated automatic armature & field voltage control for extended speed range & constant-horsepower applications. The motor is armature-voltage-controlled ...
The guy asked for suggestions on how to improve troubleshooting techniques. I mentioned this earlier as a "suggestion" for starters but the idea got lost in all the complaining and totally irrelevant responses ...
For the AC power line, the system (VFD + motor) is a non-linear load whose current include harmonics (frequency components multiples of the power line frequency). The characteristic harmonics generally ...
I have been designing power supplies for over 15 years now. We do mostly off line custom designs ranging from 50 to 500W. Often used in demanding environments such as offshore and shipping.
I think we are the ...
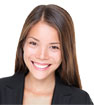
Featured
Like pumps, fans consume significant electrical energy while serving several applications. In many plants, the VFDs (variable ...
A frequency inverter controls AC motor speed. The frequency inverter converts the fixed supply frequency (60 Hz) to a ...
Motor starter (also known as soft starter, motor soft starter) is a electronic device integrates soft start, soft stop, ...
Soft starter allows the output voltage decreases gradually to achieve soft stop, in order to protect the equipment. Such as the ...
Soft Starter reduces electric motor starting current to 2-4 times during motor start up, reduces the impact to power grid during ...

In Discussion
How Much Experience Do You Have in Power Supply Design?
What Do You Do When There is No Model?
If a syn. motor run at less then syn. speed what will happening
TRANSFORMER
Anyone have experience with PVSyst for system design?
Maximum number of secondaries on a flyback converter
Comparing SCADA/HMI Software
join the solar panels of different two wattage in series?
What Do You Do When There is No Model?
If a syn. motor run at less then syn. speed what will happening
TRANSFORMER
Anyone have experience with PVSyst for system design?
Maximum number of secondaries on a flyback converter
Comparing SCADA/HMI Software
join the solar panels of different two wattage in series?