Right Half Plane Pole
Very few know about the Right Half Plane Pole (not a RHP-Zero) at high duty cycle in a DCM buck with current mode control. Maybe because it is not really a problem.
It is said that this instability starts above 2/3 duty cycle – I think that must be with a resistive load. If loaded with a pure current source, it starts above 50% duty cycle.
Here is a little down-to-earth explanation:
If you run a buck converter at high duty cycle but DCM, it probably works fine and is completely stable. Then imagine you suddenly open the feedback loop, leaving the peak current constant and unchanged. The duty cycle will then rush either back to 50% or to 100% if possible. You now have a system with a negative output resistance – if Voltage goes up, the output current will increase.
You can see it by drawing some triangles on a piece of paper: A steady state DCM current triangle with an up-slope longer than the down-slope and a fixed peak value. Now, if you imagine that the output voltage rises, you can draw a new triangle with the same peak current. The up-slope will be longer, the down-slope will be shorter but the sum of times will be longer than in the steady state case. The new triangle therefore has a larger area than the steady state triangle, which means a higher average output current. So higher output voltage generates higher output current if peak current is constant. Loaded with a current source, it is clear that this is an unstable system, like a flipflop, and it starts becoming unstable above 50% duty cycle.
However, when you close the feedback loop, the system is (conditionally) stable and the loop gain is normally so high at the RHP Pole frequency that it requires a huge gain reduction to make it unstable.
It's like when you drive on your bike. A bike has two wheels and therefore can tilt to either side – it is a system with a low frequency RHPP like a flipflop. If you stand still, it will certainly tilt to the left or to the right because you have no way to adjust your balance back. But if you drive, you have a system with feedback where you can immediately correct imbalance by turning the handlebars. As we know, this system is stable unless you have drunk a lot of beers.
It is said that this instability starts above 2/3 duty cycle – I think that must be with a resistive load. If loaded with a pure current source, it starts above 50% duty cycle.
Here is a little down-to-earth explanation:
If you run a buck converter at high duty cycle but DCM, it probably works fine and is completely stable. Then imagine you suddenly open the feedback loop, leaving the peak current constant and unchanged. The duty cycle will then rush either back to 50% or to 100% if possible. You now have a system with a negative output resistance – if Voltage goes up, the output current will increase.
You can see it by drawing some triangles on a piece of paper: A steady state DCM current triangle with an up-slope longer than the down-slope and a fixed peak value. Now, if you imagine that the output voltage rises, you can draw a new triangle with the same peak current. The up-slope will be longer, the down-slope will be shorter but the sum of times will be longer than in the steady state case. The new triangle therefore has a larger area than the steady state triangle, which means a higher average output current. So higher output voltage generates higher output current if peak current is constant. Loaded with a current source, it is clear that this is an unstable system, like a flipflop, and it starts becoming unstable above 50% duty cycle.
However, when you close the feedback loop, the system is (conditionally) stable and the loop gain is normally so high at the RHP Pole frequency that it requires a huge gain reduction to make it unstable.
It's like when you drive on your bike. A bike has two wheels and therefore can tilt to either side – it is a system with a low frequency RHPP like a flipflop. If you stand still, it will certainly tilt to the left or to the right because you have no way to adjust your balance back. But if you drive, you have a system with feedback where you can immediately correct imbalance by turning the handlebars. As we know, this system is stable unless you have drunk a lot of beers.
You may also like:
Back to electronic meters, if there are transformers inside the electronic meter, placement of a magnet as close to this transformer as possible could cause over fluxing every half a cycle, this could cause a ...
Most electric motors that suffer variations in Load already have variable frequency drives, we have capacitors installed in general switchboard to correct the reactive energy and so on. I did a discretization ...
Since one end is tied together and the two other ends are from different substations, then you will have the classic voltage sending and receiving formula. Since the load is the one substation, then their will ...
If the material is non-grain-oriented, the path of least resistance for the magnetic flux varies widely from point to point across the sheet.
If the material is grain-oriented, the material is aligned such ...
There is a ANSI/IEEE standard that defines the standard number identification for electrical devices. You will find that some of the more common ones are 50 over current, 51 short terms over current, 27 under ...
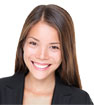
Featured
Like pumps, fans consume significant electrical energy while serving several applications. In many plants, the VFDs (variable ...
A frequency inverter controls AC motor speed. The frequency inverter converts the fixed supply frequency (60 Hz) to a ...
Motor starter (also known as soft starter, motor soft starter) is a electronic device integrates soft start, soft stop, ...
Soft starter allows the output voltage decreases gradually to achieve soft stop, in order to protect the equipment. Such as the ...
Soft Starter reduces electric motor starting current to 2-4 times during motor start up, reduces the impact to power grid during ...

In Discussion
How to select input capacitor for Phase shift controlled full bridge converter
distribution T/F of 500kva (delta-Wye) connection
Zero voltage switching
Industrial Control & Automation markets
1 megawatt ground mounted solar farm from panels to the inverters?
Why we connect Earth lead with metal tape shield in the cable?
Transmission line absorb or produce reactive power
Need Solar Inverters
distribution T/F of 500kva (delta-Wye) connection
Zero voltage switching
Industrial Control & Automation markets
1 megawatt ground mounted solar farm from panels to the inverters?
Why we connect Earth lead with metal tape shield in the cable?
Transmission line absorb or produce reactive power
Need Solar Inverters