Designing Gate drivers for IGBT
Q:
When designing gate drivers for IGBT's, how reliable are the gate driver IC's ? Now there are a lot of gate driver IC's available in the market. For example i am using the Hybrid IC M57962L for driving IGBT's for 3 phase inverter application. The peak output current of this Hybrid IC is 5A and it's written in data sheet that it can be used for driving IGBT's up to 200A, 1200V and many features in it.
For an initial design and for lower power rating the configuration is working fine. But, before going for higher power rating, i want to make sure about the reliability of Gate driver IC's in general.
Is it advisable to design gate drivers using commercially available IC's or go for a design which includes a gate drive transformer . What are the issues that may arise when using driver IC's.
A:
I've seen and developed designs using these hybrid gate drives quite successfully with long term field reliability in applications requiring from 800 V to 1.25 kV voltage isolation in power conversion products for the semiconductor capital equipment market. Powerex offers various different isolated drivers like the M57962L - my personal favorite is the VLA-502 which also contains the isolated DC/DC converter used to power the isolated gate drive electronics.
There are only two problems that I remember in the last 10 years with these types of commercial drivers - and both problems, if I remember correctly were with the stand alone DC/DC converter intended to be used with the stand alone isolated driver. One problem was a voltage isolation issue from primary to secondary inside the DC/DC switcher. Powerex acknowledged the problem, and upgraded the design. I simply do not recall the part numbers involved. The second problem was with regard to how the isolated VEE rail was established - the monopolar output of the DC/DC converter was offset negative, and ground referenced with a zener diode - and when the IGBT gate would become active at high frequency (25 kHz for that particular application), the gate charge was high enough to sag the negative supply rail against the zener shunt.
Bottom line: Use a good isolated DC/DC converter, with solid VCC and VEE regulated outputs. The isolated drivers themselves are solid in my experience - a nice, simple solution with typically better rise and fall times than gate drive transformers. They also have the added benefit of being capable of holding positive or negative DC bias if the application requires it.
When designing gate drivers for IGBT's, how reliable are the gate driver IC's ? Now there are a lot of gate driver IC's available in the market. For example i am using the Hybrid IC M57962L for driving IGBT's for 3 phase inverter application. The peak output current of this Hybrid IC is 5A and it's written in data sheet that it can be used for driving IGBT's up to 200A, 1200V and many features in it.
For an initial design and for lower power rating the configuration is working fine. But, before going for higher power rating, i want to make sure about the reliability of Gate driver IC's in general.
Is it advisable to design gate drivers using commercially available IC's or go for a design which includes a gate drive transformer . What are the issues that may arise when using driver IC's.
A:
I've seen and developed designs using these hybrid gate drives quite successfully with long term field reliability in applications requiring from 800 V to 1.25 kV voltage isolation in power conversion products for the semiconductor capital equipment market. Powerex offers various different isolated drivers like the M57962L - my personal favorite is the VLA-502 which also contains the isolated DC/DC converter used to power the isolated gate drive electronics.
There are only two problems that I remember in the last 10 years with these types of commercial drivers - and both problems, if I remember correctly were with the stand alone DC/DC converter intended to be used with the stand alone isolated driver. One problem was a voltage isolation issue from primary to secondary inside the DC/DC switcher. Powerex acknowledged the problem, and upgraded the design. I simply do not recall the part numbers involved. The second problem was with regard to how the isolated VEE rail was established - the monopolar output of the DC/DC converter was offset negative, and ground referenced with a zener diode - and when the IGBT gate would become active at high frequency (25 kHz for that particular application), the gate charge was high enough to sag the negative supply rail against the zener shunt.
Bottom line: Use a good isolated DC/DC converter, with solid VCC and VEE regulated outputs. The isolated drivers themselves are solid in my experience - a nice, simple solution with typically better rise and fall times than gate drive transformers. They also have the added benefit of being capable of holding positive or negative DC bias if the application requires it.
You may also like:
Many of the techniques contributed by others in the discussion address faults, but how do you address the "normal" things that can hold up an action such as waiting for a process condition to occur, such as ...
If referring to the acoustic noise generated at or around the PWM frequency of the inverter, then you may notice a very slight difference between "BLDC" and an induction motor. Assume that it's referring to a ...
This is a very simplified comparison for a very complex issue. Every manufacturer is somewhat different in their approach, and there are literally thousands of design details in each machine that can be ...
I once uprated a set of 3x 500KVA 11/.433kv ONAN transformers to 800KVA simply by fitting bigger radiators. This was with the manufacturers blessing. (not hermetically sealed - there were significant ...
Babbitt Bearings, properly cared for and maintained will last much longer than anti-friction bearings. Properly set up and aligned there is no contact between the babbitt and the journal other that a scuff ...
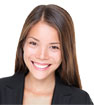
Featured
Like pumps, fans consume significant electrical energy while serving several applications. In many plants, the VFDs (variable ...
A frequency inverter controls AC motor speed. The frequency inverter converts the fixed supply frequency (60 Hz) to a ...
Motor starter (also known as soft starter, motor soft starter) is a electronic device integrates soft start, soft stop, ...
Soft starter allows the output voltage decreases gradually to achieve soft stop, in order to protect the equipment. Such as the ...
Soft Starter reduces electric motor starting current to 2-4 times during motor start up, reduces the impact to power grid during ...

In Discussion
loose connections at the motor Junction Box
Can standard electric motor be coupled with VFD?
how to calculate length from ppr of an encoder????
Questions about direct torque control
Suction Piping Design Guidelines
Maximum value of Space Vector in Field oriented control of BLDC motors
Logic behind RMS conversion.
PCB Layout Rules and Experiences
Can standard electric motor be coupled with VFD?
how to calculate length from ppr of an encoder????
Questions about direct torque control
Suction Piping Design Guidelines
Maximum value of Space Vector in Field oriented control of BLDC motors
Logic behind RMS conversion.
PCB Layout Rules and Experiences