SCADA & HMI
SCADA will have a set of KPI's that are used by the PLCs/PACs/RTUs as standards to compare to the readings coming from the intelligent devices they are connected to such as flowmeters, sensors, pressure guages, etc.
HMI is a graphical representation of your process system that is provided both the KPI data and receives the readings from the various devices through the PLC/PAC/RTUs. For example you may be using a PLC that has 24 i/o blocks that are connected to various intelligent devices that covers part of your water treatment plant. The HMI software provides the operator with a graphical view of the treatment plant that you customize so that your virtual devices and actual devices are synchronized with the correct i/o blocks in your PLC. So, when an alarm is triggered, instead of the operator receiving a message that the 15th i/o block on PLC 7 failed, you could see that the pressure guage in a boiler reached maximum safety level, triggering a shutdown and awaiting operator approval for restart.
Here is some more info I got from my colleague who is the expert in the HMI market, this is a summary from the scope of his last market study which is about a year old.
HMI software's complexity ranges from a simple PLC/PAC operating interface but as plant systems have evolved, HMI functionality and importance has as well. HMI is an integral component of a Collaborative Production Management (CPM) system; simply you can define that as the integration of Enterprise, Operations, and Automation software into a single system. Collaborative Production Systems (CPS) require a common HMI software solution that can visualize the data and information required at this converged point of operations and production management. HMI software is the bridge between your Automation Systems and Operations Management systems.
An HMI software package typically performs functions such as process visualization and animation, data acquisition and management, process monitoring and alarming, management reporting, and database serving to other enterprise applications. In many cases, HMI software package can also perform control functions such as basic regulatory control, batch control, supervisory control, and statistical process control.
"Ergonometrics," where increased ergonomics help increase KPI and metric results, requires deploying the latest HMI software packages. These offer the best resolution to support 3D solutions and visualization based on technologies such as Microsoft Silverlight. Integrating real-time live video into HMI software tools provide another excellent opportunity to maximize operator effectiveness. Live video provides a "fourth dimension" for intelligent visualization and control solutions. Finally, the need for open and secure access to data across the entire enterprise drives the creation of a single environment where these applications can coexist and share information. This environment requires the latest HMI software capable of providing visualization and intelligence solutions for automation, energy management, and production management systems.
HMI is a graphical representation of your process system that is provided both the KPI data and receives the readings from the various devices through the PLC/PAC/RTUs. For example you may be using a PLC that has 24 i/o blocks that are connected to various intelligent devices that covers part of your water treatment plant. The HMI software provides the operator with a graphical view of the treatment plant that you customize so that your virtual devices and actual devices are synchronized with the correct i/o blocks in your PLC. So, when an alarm is triggered, instead of the operator receiving a message that the 15th i/o block on PLC 7 failed, you could see that the pressure guage in a boiler reached maximum safety level, triggering a shutdown and awaiting operator approval for restart.
Here is some more info I got from my colleague who is the expert in the HMI market, this is a summary from the scope of his last market study which is about a year old.
HMI software's complexity ranges from a simple PLC/PAC operating interface but as plant systems have evolved, HMI functionality and importance has as well. HMI is an integral component of a Collaborative Production Management (CPM) system; simply you can define that as the integration of Enterprise, Operations, and Automation software into a single system. Collaborative Production Systems (CPS) require a common HMI software solution that can visualize the data and information required at this converged point of operations and production management. HMI software is the bridge between your Automation Systems and Operations Management systems.
An HMI software package typically performs functions such as process visualization and animation, data acquisition and management, process monitoring and alarming, management reporting, and database serving to other enterprise applications. In many cases, HMI software package can also perform control functions such as basic regulatory control, batch control, supervisory control, and statistical process control.
"Ergonometrics," where increased ergonomics help increase KPI and metric results, requires deploying the latest HMI software packages. These offer the best resolution to support 3D solutions and visualization based on technologies such as Microsoft Silverlight. Integrating real-time live video into HMI software tools provide another excellent opportunity to maximize operator effectiveness. Live video provides a "fourth dimension" for intelligent visualization and control solutions. Finally, the need for open and secure access to data across the entire enterprise drives the creation of a single environment where these applications can coexist and share information. This environment requires the latest HMI software capable of providing visualization and intelligence solutions for automation, energy management, and production management systems.
You may also like:
The harmonics are created by the loads that the transformer supplies power to. If your loads include a high percentage of electronic loads like IT equipment, electronic ballast lighting, electronic motor ...
In order to do an extensive and credible study to explore renewable energy potential in each Taluka, State and Central Government Can hire international Consultancies with Video Documentation with GPRS MAPS to ...
A typical variable torque application would be a centrifugal pump. A typical constant torque application would be a conveyor, and there are positive displacement pumps that are also constant torque. Have a ...
EMI/EMC is rather a subjective topic than theoretic, but we shall look at it with start from noise prevention then noise suppression.
Prevention or design in the solution is needed to concentrate on noise ...
Usually in your case there should be Electrical as well as Mechanical interlocks between the mains incomer & genset main breaker. ie both Sources will never be in Synchronism ( will not feeding the same ...
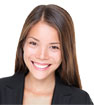
Featured
Like pumps, fans consume significant electrical energy while serving several applications. In many plants, the VFDs (variable ...
A frequency inverter controls AC motor speed. The frequency inverter converts the fixed supply frequency (60 Hz) to a ...
Motor starter (also known as soft starter, motor soft starter) is a electronic device integrates soft start, soft stop, ...
Soft starter allows the output voltage decreases gradually to achieve soft stop, in order to protect the equipment. Such as the ...
Soft Starter reduces electric motor starting current to 2-4 times during motor start up, reduces the impact to power grid during ...

In Discussion
BS standard BS-7430
Hubble Power Supply Failure
MAXIMUM POWER TRANSFER during Grid Synchronization
Canonical form of DC converter
how to do load (torque) sharing with Allen Bradley servos?
What is the role of VARS in system voltage improvement?
What packaging is used to ship PV panels to their installation location?
VFD DBR and Active front end
Hubble Power Supply Failure
MAXIMUM POWER TRANSFER during Grid Synchronization
Canonical form of DC converter
how to do load (torque) sharing with Allen Bradley servos?
What is the role of VARS in system voltage improvement?
What packaging is used to ship PV panels to their installation location?
VFD DBR and Active front end